Enterprise Asset Management (EAM) is ushering in a new era of efficiency in manufacturing. By enabling better tracking and utilization of assets, EAM optimizes operations, reduces downtime, and drives profitability. However, successful EAM implementation demands more than just digitization—it requires strategic planning, effective use of technology, and a commitment to continuous improvement.
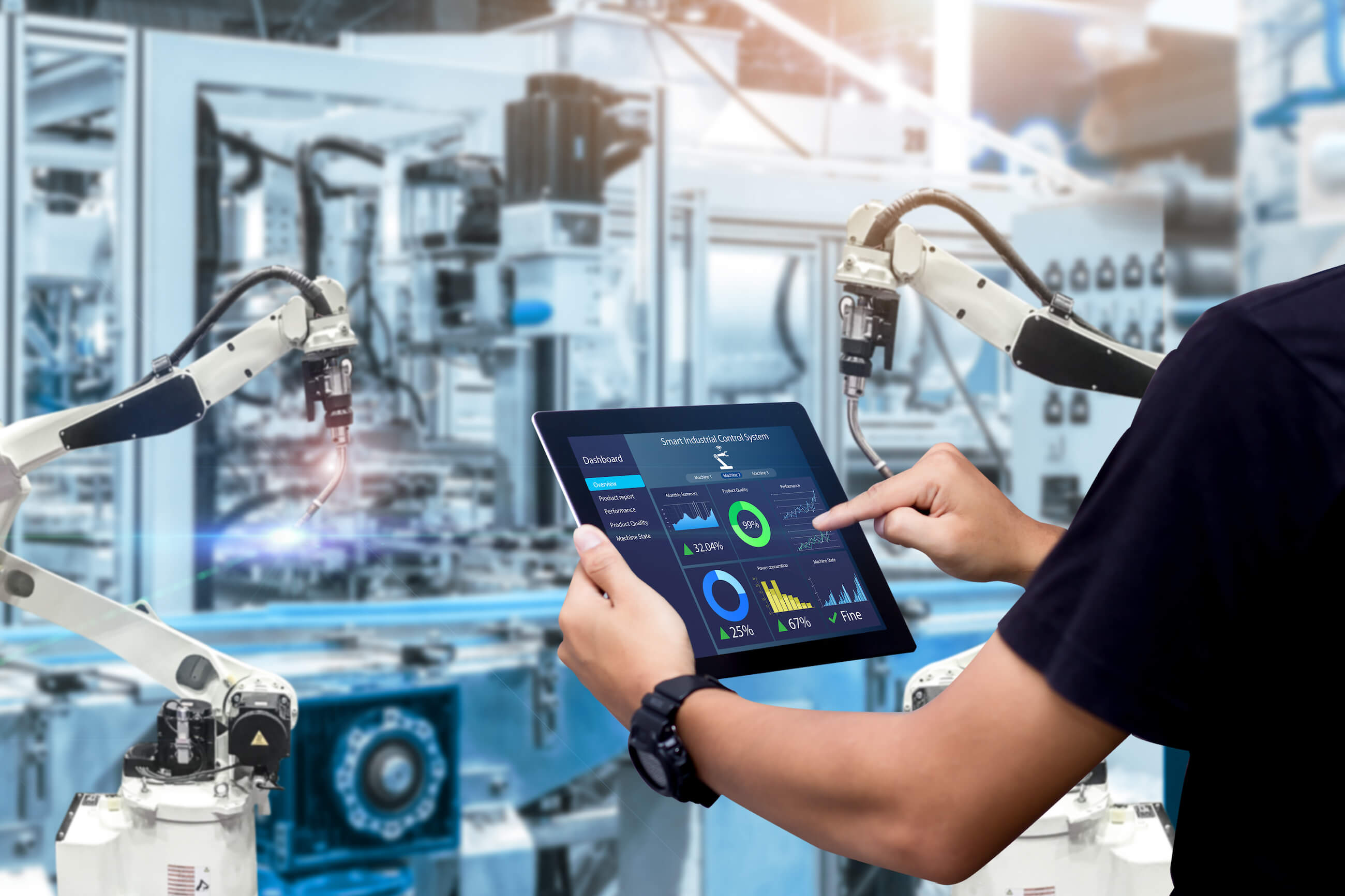
The Age of Digital Transformation
The concept of EAM isn't new, but its potential has been truly unleashed in the age of Industry 4.0. As digitization sweeps across the manufacturing sector, EAM systems have evolved to become more advanced, offering features like real-time tracking, predictive maintenance, and advanced data analytics.
Yet, the digital transformation goes beyond simply implementing new technologies. It's about harnessing digital tools to redefine processes, drive operational efficiency, and enhance customer service.
The digital transformation is about more than just adding new technologies. It's about using digital tools to redefine processes and drive efficiency.
In this context, predictive maintenance plays a crucial role. By predicting potential asset failures before they occur, manufacturers can minimize downtime, reduce costs, and enhance operational efficiency.
Challenges in Asset Management
As promising as it sounds, implementing an effective EAM system isn't without challenges. The first hurdle often lies in the digitization process itself. Despite the clear benefits of digitization, many manufacturers struggle to embark on this journey due to operational complexities and the perceived high costs of technological investment.
Understanding machine downtime is another challenge. Downtime is a significant drain on resources, and yet, it remains poorly understood and inadequately managed in many manufacturing setups.
Then, there are issues related to data management. With the proliferation of data in today's digital age, managing and making sense of this data is a significant challenge.
A Framework for Effective EAM
Implementing an effective EAM system requires a strategic approach. It starts with understanding the current state of assets and identifying the areas where digital tools can add value. Then, comes the phase of selecting the right tools, implementing them, and monitoring their performance to ensure they deliver the desired outcomes.
A cornerstone of this framework is the Smart Service Platform. It provides a comprehensive suite of services for digitizing after-sales services and customer support. This includes a ticketing system for efficient problem resolution and a parts service for managing spare parts.
The importance of training can't be overstated when implementing an EAM system. As part of the digitization process, training staff on using new digital tools is crucial for the successful adoption of these technologies. Here, the role of education and training with remote support can't be overstated.
The Impact of EAM
EAM is more than just a tool for managing assets—it's a strategic enabler for achieving operational efficiency and customer service excellence. By implementing an effective EAM system, manufacturers can reduce costs, improve efficiency, enhance customer satisfaction, and drive bottom-line results.
The journey towards effective enterprise asset management may be complex, but with the right approach and tools, it's a journey worth taking. After all, in today's digital age, EAM is not just a competitive advantage—it's a business imperative.
How Modern EAM Systems are Transforming Manufacturing
We discussed the importance of Enterprise Asset Management (EAM) and the challenges manufacturers face when implementing it. Let's now delve into how modern EAM systems are reshaping the manufacturing industry, and how you can leverage these tools for success.
Harnessing the Power of Data
As manufacturing becomes increasingly digitized, manufacturers are finding themselves in the midst of a data deluge. Fortunately, modern EAM systems are well-equipped to handle this data influx. They collect and analyze data from various sources, providing valuable insights that can drive strategic decisions.
For instance, by leveraging data, manufacturers can predict when a machine is likely to fail and take proactive steps to prevent it, reducing costly downtime. The predictive maintenance capabilities of modern EAM systems are key to this process.
The rise of artificial intelligence in manufacturing is also playing a critical role in asset management. By integrating AI with EAM, manufacturers can achieve more accurate predictions, optimize maintenance schedules, and improve asset utilization.
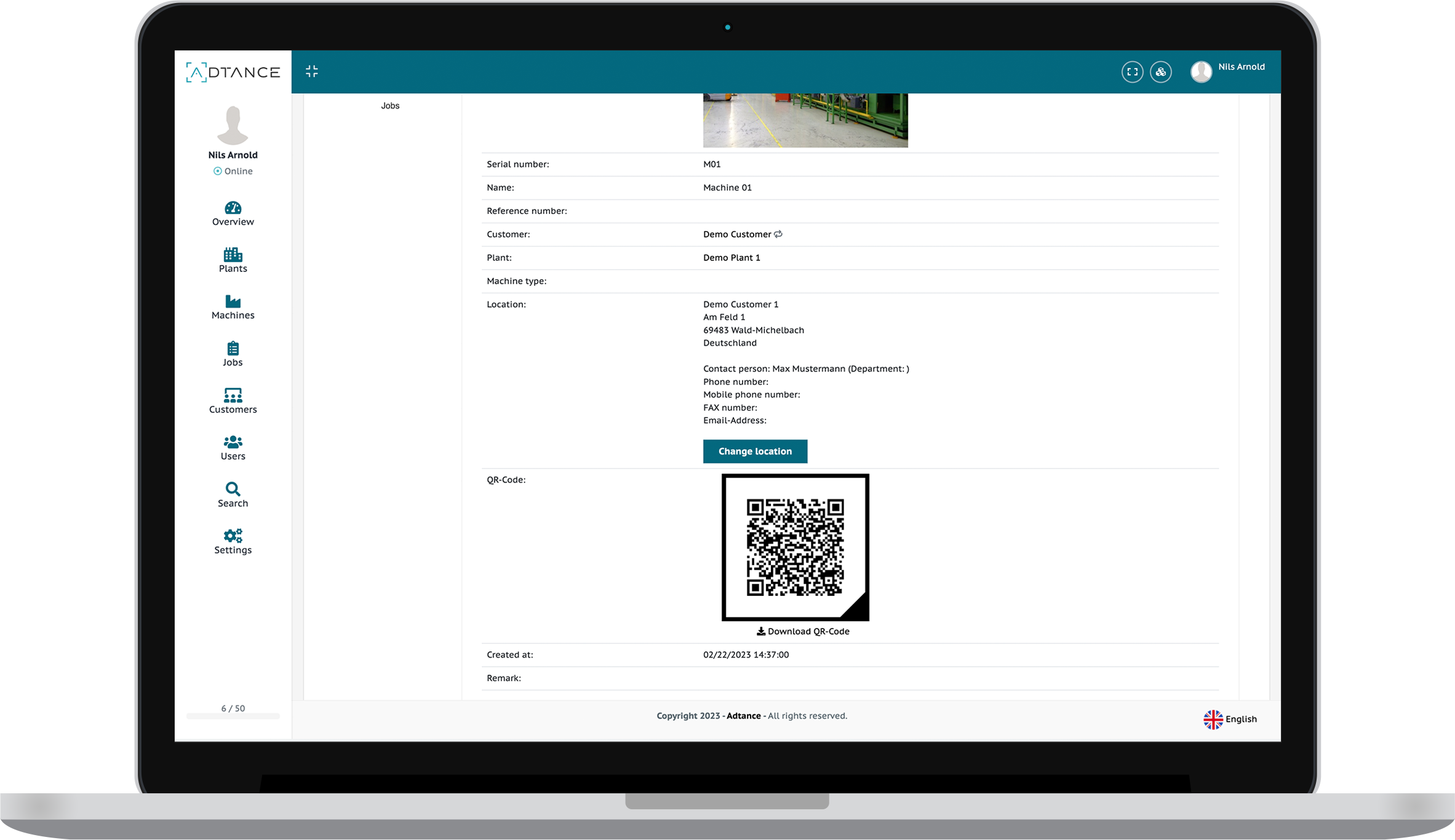
The integration of AI with EAM is revolutionizing asset management, enabling more accurate predictions, optimized maintenance schedules, and improved asset utilization.
The Role of Remote Support
Remote support has emerged as a game-changer in EAM. With remote support, manufacturers can monitor and manage assets from anywhere, at any time. This not only reduces the need for on-site visits but also enables faster resolution of issues.
Our Smart Services Support plays a pivotal role here. It offers tools for remote video support, helping manufacturers resolve issues quickly and effectively, even from afar.
EAM and Customer Satisfaction
While EAM is primarily about managing assets, it also has a profound impact on customer satisfaction. After all, efficient asset management leads to better product quality, shorter delivery times, and more reliable service—all of which contribute to customer satisfaction.
Hence, while implementing an EAM system, manufacturers need to keep the customer perspective in mind. This involves understanding the 5 steps to improve customer satisfaction and incorporating these principles into the asset management strategy.
Towards a More Sustainable Future
Finally, it's worth noting that EAM isn't just about improving profitability—it's also about sustainability. By helping manufacturers optimize resource use, reduce waste, and extend asset life, EAM contributes to a more sustainable manufacturing sector.
A prime example of this is retrofit digitization. By retrofitting old machines with digital technologies, manufacturers can extend their lifespan, reduce waste, and make a positive contribution to the environment.
Optimizing Enterprise Asset Management in the Age of Industry 4.0
After exploring the importance of Enterprise Asset Management (EAM) and the advancements brought by modern systems, it's crucial to address implementation. After all, the benefits of EAM can only be realized through effective and seamless deployment.
Seamless Integration is the Key
Effective EAM isn't a standalone function—it's intricately connected with various aspects of a manufacturing business. As such, integration with other systems is critical.
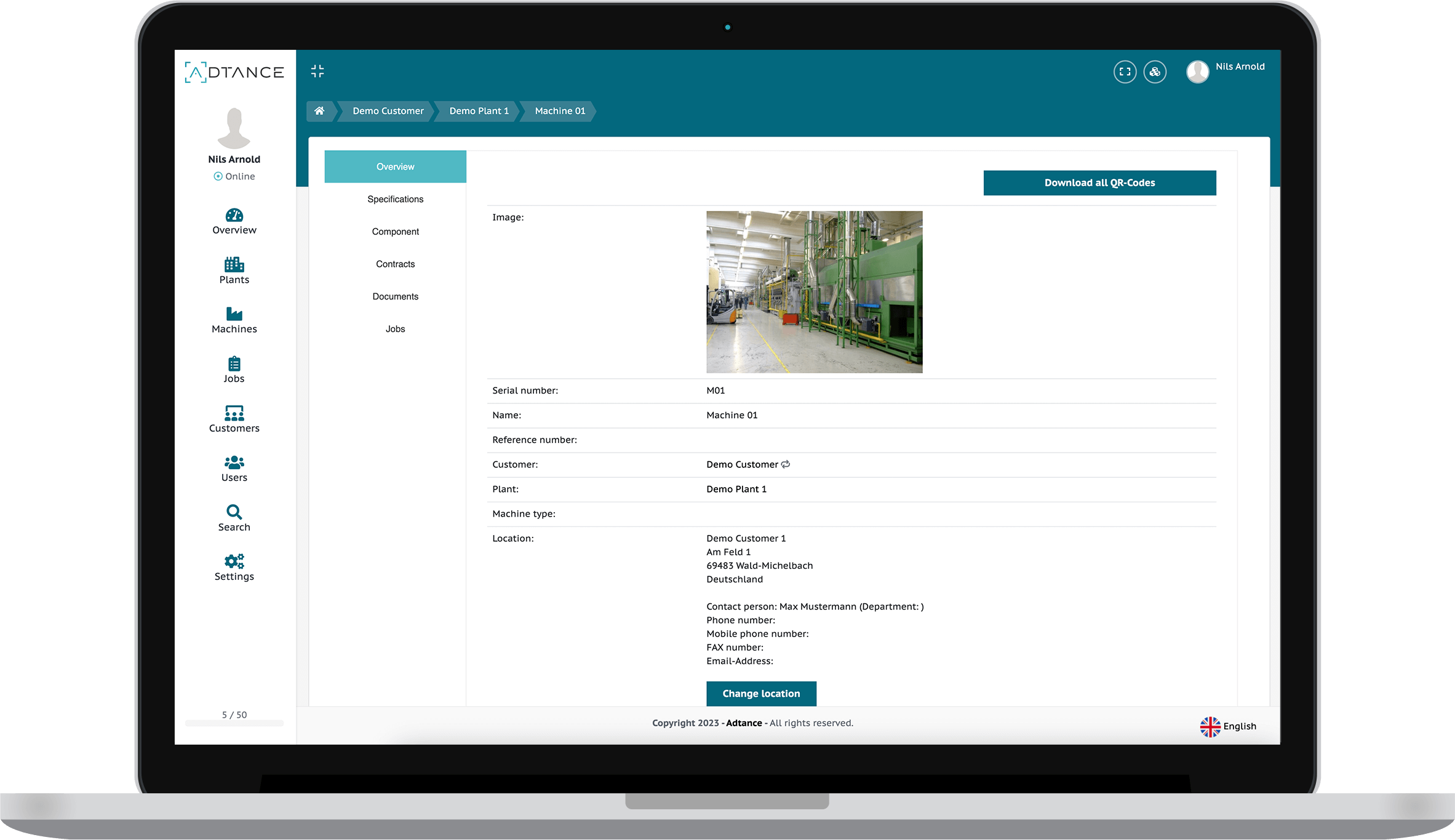
For example, integrating the EAM system with the service platform can streamline workflows, improve response times, and enhance customer service. Moreover, by connecting EAM with systems like Parts Management and Ticketing, manufacturers can get a holistic view of their operations, improving decision-making.
However, integrating disparate systems can be complex. It's vital to ensure data consistency, avoid duplication, and maintain security during this process. Also, manufacturers need to be aware of the 5 mistakes when implementing a customer portal to ensure a smooth and effective integration.
Digital Training is Essential
As with any technology, the benefits of EAM can only be reaped if employees know how to use it. Therefore, digital training is an integral part of EAM implementation.
Digital training can take various forms, from online tutorials to interactive simulations. However, the key is to make it engaging, practical, and relevant. Remember that education and training with remote support can greatly enhance the learning experience.
Effective digital training can ensure employees fully leverage the benefits of EAM, leading to improved productivity and efficiency.
Embrace Change, But Don't Rush
Transitioning to a new EAM system represents a significant change, and it's crucial to manage this change effectively. This involves communicating the benefits of the new system, addressing any concerns, and providing adequate support during the transition period.
However, while it's important to embrace change, it's equally important not to rush it. After all, implementing an EAM system is a major undertaking and it's crucial to get it right. As such, it's advisable to adopt a phased approach, starting small and gradually scaling up as the organization becomes more comfortable with the new system.
Leverage Industry 4.0
Finally, to fully capitalize on EAM, manufacturers need to embrace Industry 4.0. This includes leveraging technologies like Augmented Reality, which can revolutionize asset management, providing immersive and interactive experiences that enhance efficiency and accuracy.
In conclusion, optimizing EAM in the age of Industry 4.0 requires a strategic approach—one that combines effective integration, comprehensive training, careful change management, and a willingness to embrace new technologies. By doing so, manufacturers can not only optimize asset management but also drive growth, profitability, and sustainability in a rapidly evolving industry landscape.