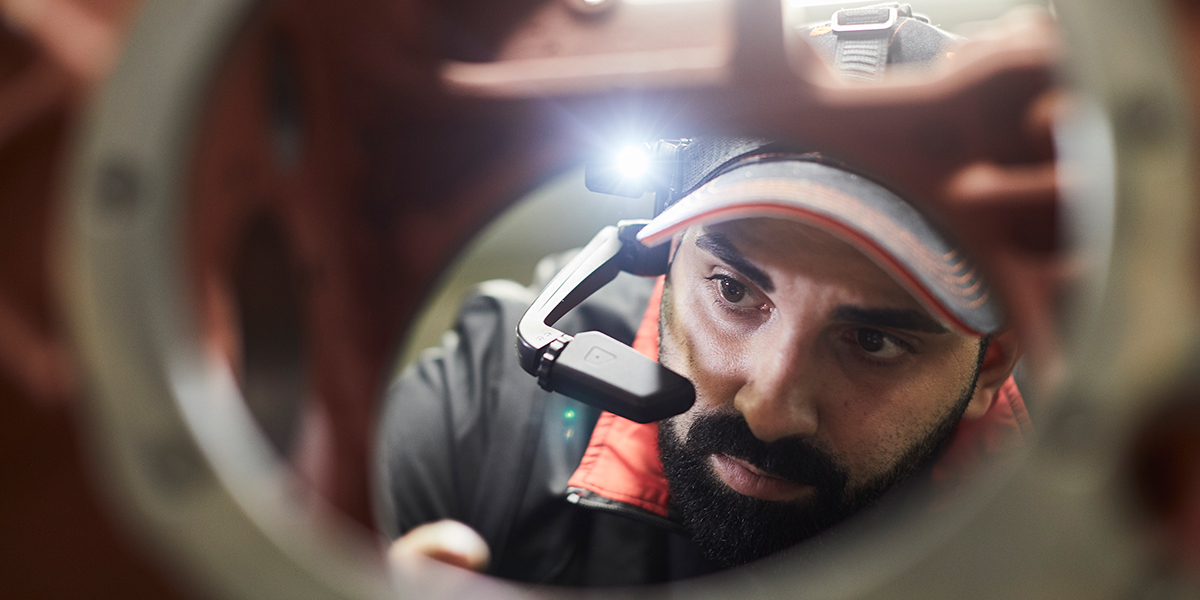
The Component Approval Process
Component Approval Today
For special components of a system or plant, a component approval may be necessary. Either because it was agreed between customer and manufacturer as the last step in quality assurance or because it is required by law. This is particularly the case for safety-relevant components, where the approval not only serves the purpose of quality assurance, but is also important for both sides for possible recourse claims in the event of damage.
For this purpose, an authorized expert or the customer himself must travel to the manufacturing company in order to jointly carry out and document the acceptance and to jointly sign the approval protocol. This is always associated with a large expenditure of time for the arrival and departure. In addition, there are costs for travel time, means of transport and overnight stay.
Corona and the Obstacles of Contact Restrictions
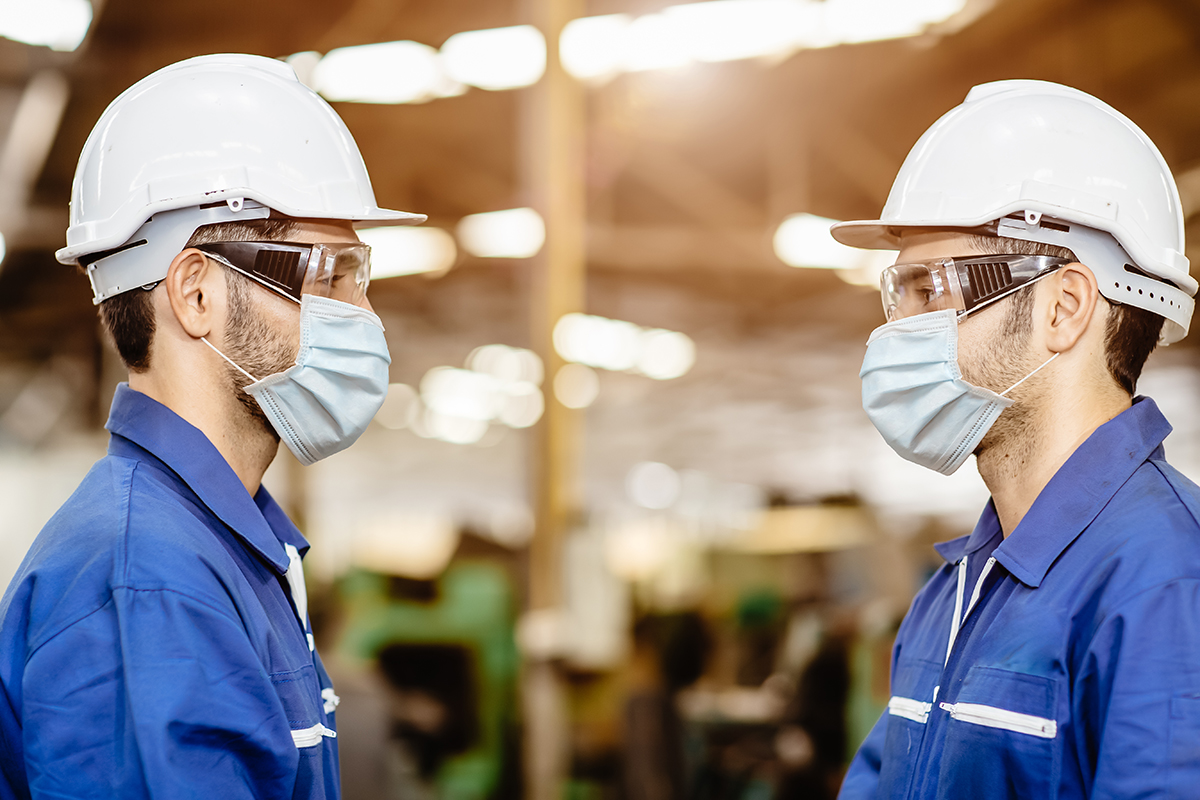
While it has always been very cumbersome to carry out this type of approval, Corona made it impossible at times. Due to the complete contact restrictions during the lockdown from March onwards, travel was sometimes not feasible. And even now there are still many companies that only allow their employees to travel in exceptional cases.
Other companies, on the other hand, still do not allow employees of external companies or visitors on the factory premises. A situation that continues to cause a lot of downtime in the industry. And it is not yet foreseeable how long this situation will last.
Component Approval via Live Stream
One solution is the use of remote maintenance software. It is not only suitable for remote maintenance and commissioning of complex machines and plants, but also for the acceptance of components without direct customer contact. In a video live stream, buyers and manufacturers can meet virtually in order to work together on the approval of components in all necessary steps.
Procedure
In advance, the customer or the acceptance specialist has received a session number for a remote support session from the component manufacturer. Only with this number he gets access to the session. It is thus protected against access by third parties. Several employees of the customer can also participate in the session with this number. They can watch on their laptop, tablet or even smartphone via virtual shoulder view in the live stream how the employee of the manufacturer performs the approval. During component acceptance, the employee of the component manufacturer wears a Smart Glass. He has his hands free and can act in the same way as he would in an approval process with direct customer contact. The employee and the customer can talk to each other. The customer can point out specific points that he wants to see in detail. For this purpose he can mark individual parts on his monitor. This marking appears in the employee's field of vision, so that the employee can see exactly what the customer is looking at in the Smart Glass. For documentation purposes, partial steps of the acceptance procedure can be recorded as a picture or video recording.
Step by step, the approval takes place in front of the customer's eyes with the same quality and precision as in a conventional inspection. The customer can approve it directly afterwards, so that the component is released and can be dispatched.
Advantages of the Remote Maintenance Software
The use of the software results in a number of advantages, not all of which are so obvious at first glance, such as savings in travel and accommodation costs.
Making Better use of Employee Capacity
The employee who is to accompany the approval can now follow it from his office or home office. Not only the costs for the journey are eliminated.
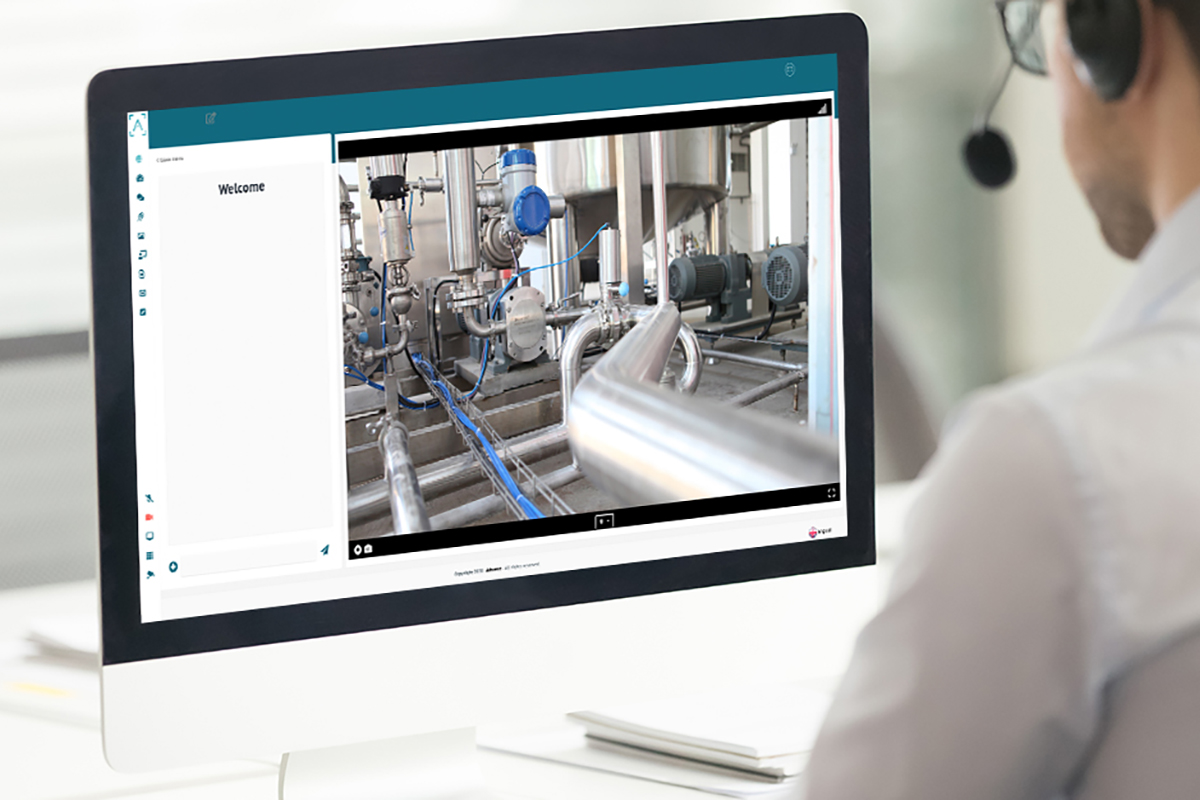
Also the usually unused travel time is eliminated and the availability of the employee increases. The video stream can be integrated into the normal working day. Thus the employee can take care of the daily business despite the decrease and does not have to be absent because of travel - in the worst case for several days. By sharing the session number, several employees can easily take part in the approval process. With a conventional approval, this would drive up costs. For example, new employees can easily be familiarized with the processes of an approval.
If there are any uncertainties during the approval process, a specialist or colleague can be spontaneously called in; an option that normally does not exist. Under the usual conditions of an on-site approval, such a situation would lead to the cancellation of the approval. It would have to be continued at a different time after clarification of the facts. This would lead to a new loss of time, which could delay an entire project, and to new travel costs. A risk that can be significantly minimized by the acceptance with remote support.
Optimizing Resources
Resources are also saved on the side of the component manufacturer. The time required is also significantly reduced here, so that one buyer can carry out several approvals per day. If the customer is physically on site at the manufacturer's plant, it is more difficult to carry out the approval at close intervals. The risk of delays in acceptance due to traffic jams and unplanned waiting time for the customer is completely eliminated. In addition to these positive aspects for all parties, the reduction of business trips and the associated CO2 savings make the acceptance process more sustainable.
Successful in Use - Testing of Safety Valves
Many companies have already recognized the numerous advantages of using the software not only for remote maintenance. It is used in a wide variety of industries to simplify the daily work of operators and make it more efficient.
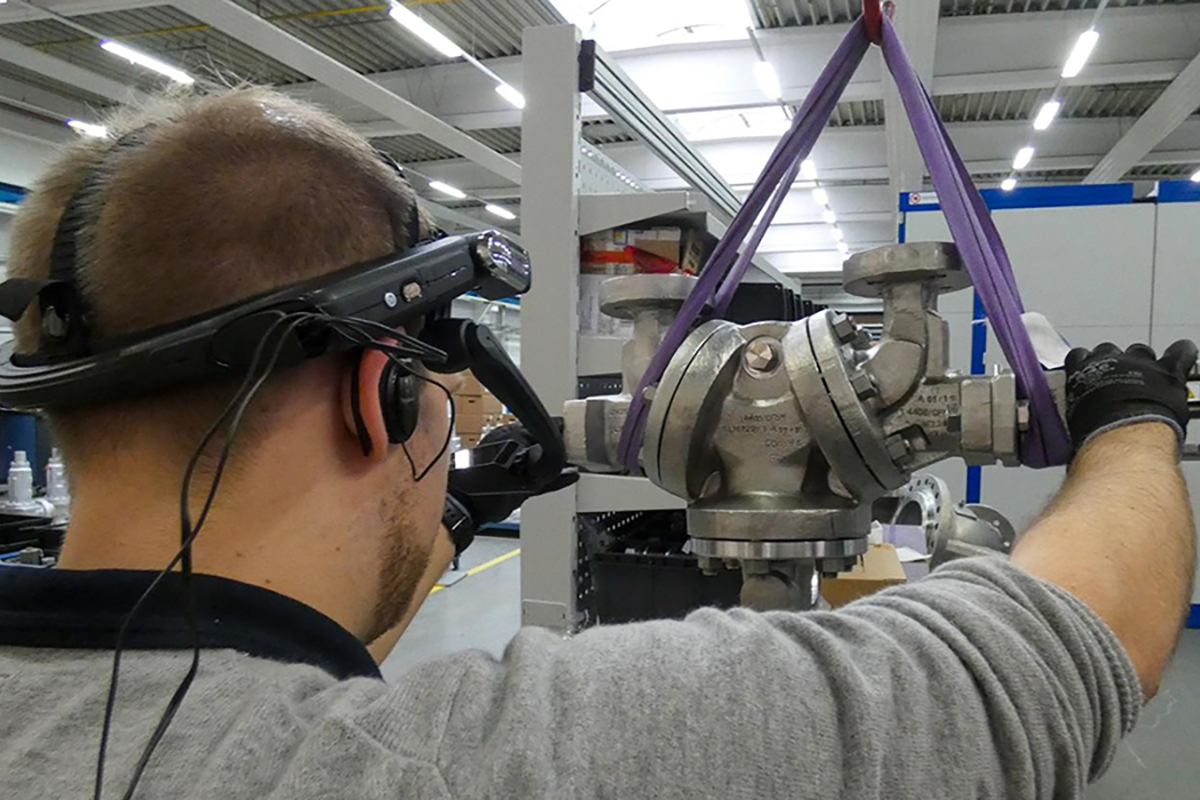
LESER, the internationally active industry leader for safety valves, also performs the component approval of their safety valves in live stream with the help of remote maintenance software and the RealWear HMT-1 smart glasses. With these smart glasses the customer shares his field of vision with the customer and the common acceptance can be carried out as usual.
LESER has been involved in the topic of remote maintenance long before the pandemic became apparent and introduced the software even before the outbreak of Corona. One of the goals achieved with the introduction was to increase the availability of the inspectors. With the beginning of the contact restrictions, LESER was nevertheless able to continue production through the software and to continue to accept the produced safety valves with the customers. The fact that the approval could be carried out without contact was an advantage that nobody had thought of during the introduction. You can read in detail how the component approval is implemented at LESER using the remote maintenance software in the LESER customer success story.