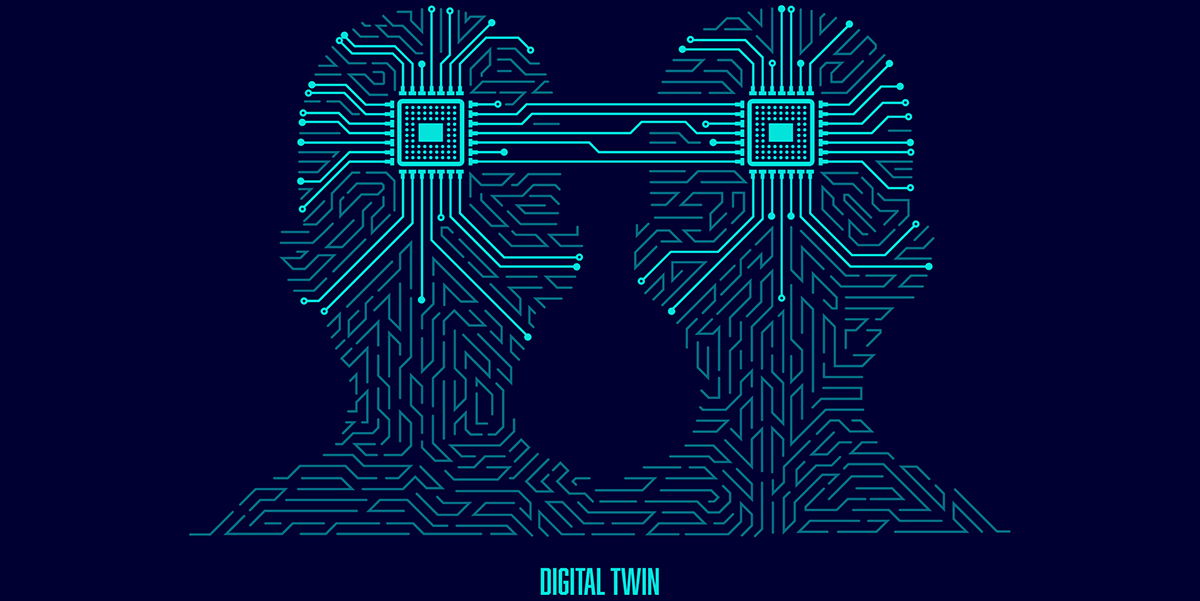
You can reveal hidden opportunities for improvement in your manufacturing process. You can accomplish this feat with a digital twin. The IoT, digital twin, and smart factory technologies are expanding their roles. They’re finding a prominent place in manufacturing and supply chain operations. The popularity of these technologies has grown considerably in recent years.
More decision-makers are learning that using digital twin technology is invaluable. The technology enables manufacturers to replicate and assess their entire footprint digitally. More importantly, it enables them to identify and resolve pain points.
To learn more about the digital twin in the manufacturing industry, keep reading.
What Is a Digital Twin?
Digital twin technology enables stakeholders to test different solutions. It allows them to see how things perform before using them in the real world. A digital twin is a digital replica. Typically, it mimics a physical object or system.
Now, however, engineers have expanded the technology for use in massive applications. For example, firms have deployed digital twins to analyze buildings and factories. In some cases, they even use digital twin technology to evaluate cities.
Most remarkably, medical researchers are exploring the concept of using digital twins. They’re using the tech to evaluate the human body. This application will expand the use of the digital twin even more.
The idea of the digital twin started with NASA. In the past, the agency created full-scale markups of early space equipment. They tested the equipment on the ground. The markups enabled NASA scientists to mirror and diagnose potential problems in orbit. Over time, this process evolved into digital simulations.
In recent years, analysts have singled out digital twin technology. They’ve identified it as one of the top ten innovations in the world. Technology watchdogs forecast that firms will soon replicate billions of things. The use of digital twins will soon become the norm. Now, there are tens of billions of sensors and endpoints connected by the Internet of Things (IoT). These endpoints open up yet another realm of possibility for digital twin technology.
Digital Twins, the IoT, Big Data and Companies
In recent years, there’s been an explosion of IoT sensors. In part, this sharp upsurge in IoT endpoints has ushered in the latest era of digital twin case uses. Now, IoT devices are more refined. Resultantly, digital twin scenarios might include smaller and less complex objects. The scenarios provide additional benefits to companies.
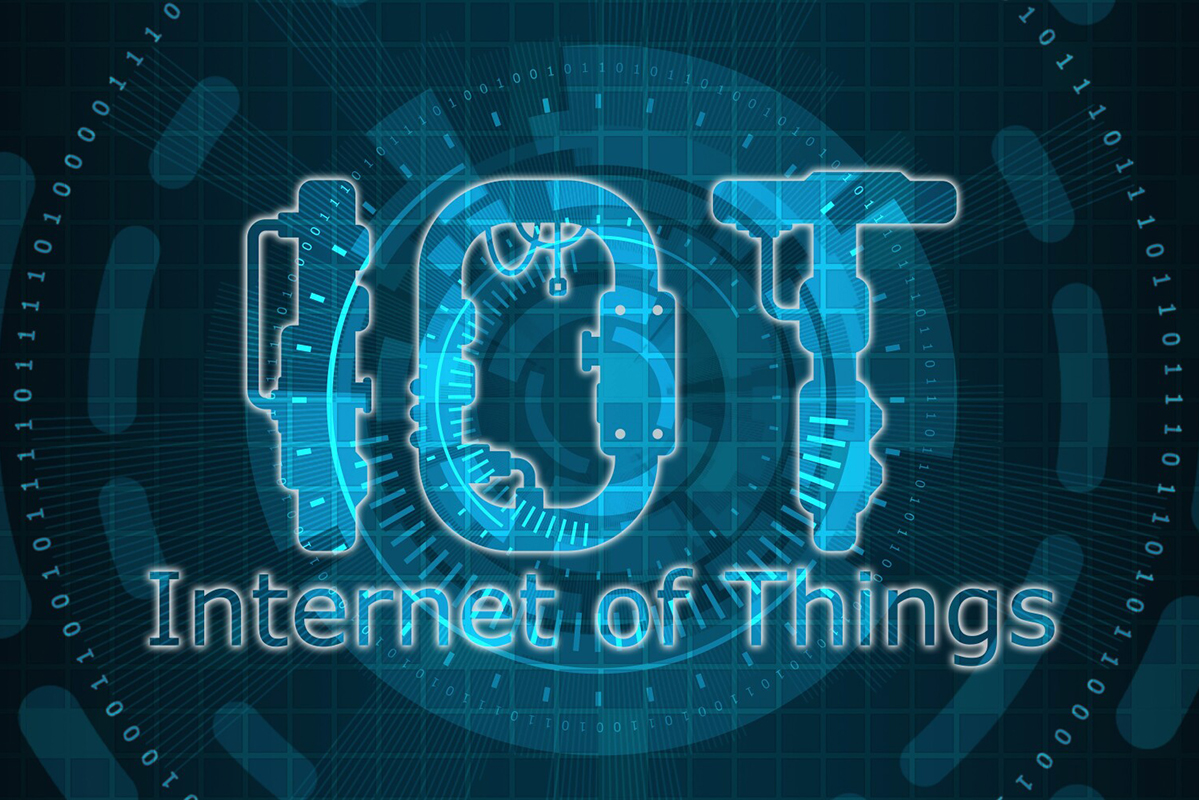
Digital twins enable companies to predict various outcomes. The technology bases these outcomes on variable data.
Digital twin systems run various scenarios. Part of the digital twin system runs on data analytics. The systems prove scenarios in a digital environment. Often, engineers use digital twins for IoT deployment. The technology helps to ensure maximum efficiency.
For example, digital twins help engineers to figure out where to place devices. It also helps them to figure out how the devices will perform before they deploy them in the real world. It’s important that a digital twin duplicates a physical object as closely as possible. In this way, it can find hidden inefficiencies as well as benefits. More importantly, a realistic digital twin can help engineers to forecast performance over time. This ability can help engineers to assess future performance and potential failures.
Use Cases of the Digital Twin in Manufacturing
Today, there are many applications for digital twin technology. As an example, there are two well-established applications for digital twins. These applications include automobiles and maritime vessels. Engineers also use digital twins to test other constructs. These constructs might consist of aircraft engines and trains. They even use them to evaluate offshore platforms and turbines. With digital twin technology, they can test this kind of complex equipment digitally.
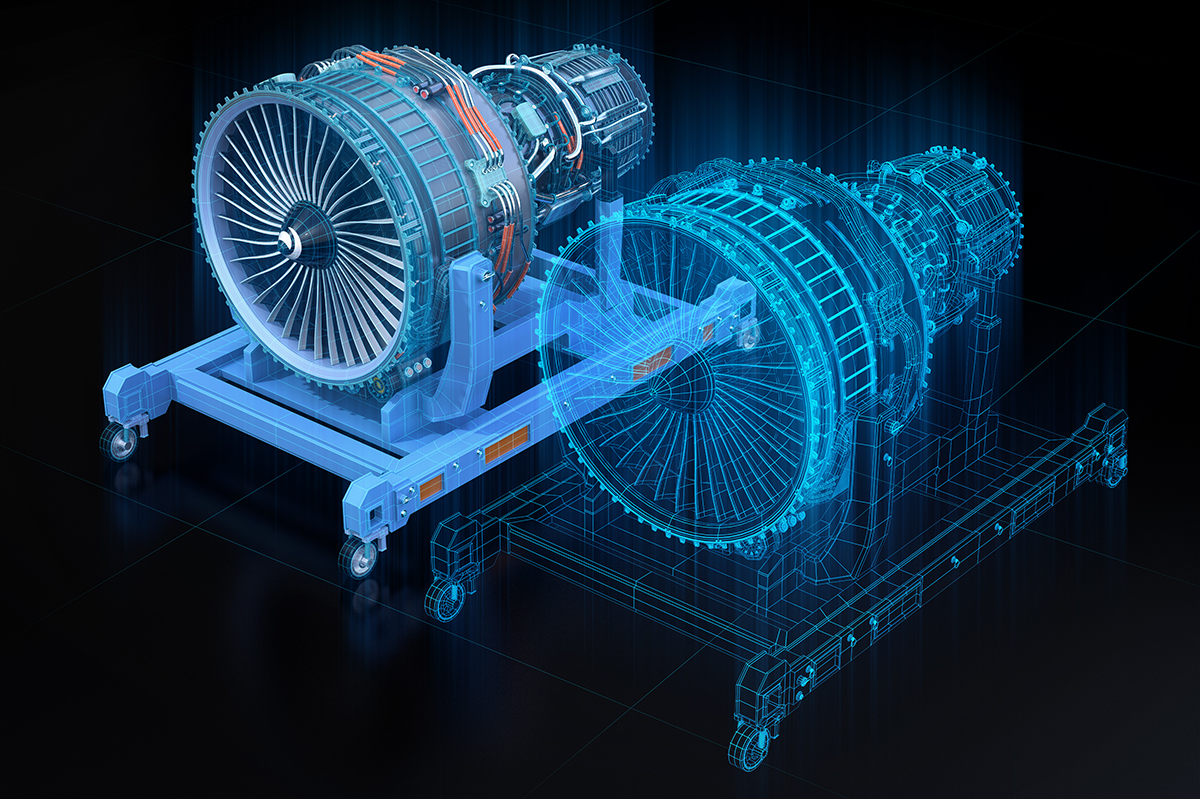
More importantly, engineers can use digital twins to diagnose problems. It allows them to detect issues before building a physical good. Digital twins can also help engineers resolve maintenance issues. As an example, a technician can use a digital twin to test a proposed repair for equipment.
The simulation will help the technician to assess whether the fix will work. It saves them from applying a faulty fix in the real world.
With this application, digital twin technology helps technicians reduce operating costs.
Other Uses for Digital Twin Technology
There are also many applications for digital twins in the business world. So far, however, the technology is most prominent in discrete manufacturing fields. Many factories use digital twins to simulate their processes. The automotive field has an advantage, however, regarding digital twin technology. Cars are already outfitted with a considerable amount of telemetry sensors.
More autonomous vehicles are going into service. As this happens, it will become more important to refine the technology. Digital twins can aid with the process. On the cutting-edge of science, medical researchers are exploring digital twin technology. In medicine, the process of using digital twins involves band-aid sized sensors.
The sensors send information back to the digital twin. Technicians can then use that information to monitor and protect a patient’s health.
Why Digital Twin Technology Matters in Manufacturing
In manufacturing, digital twin technology is disrupting the sector. Here, the deployment of digital twin technology is most prominent. Engineers are using digital twin technology to address quality. They’re also using it to evaluate performance issues for physical products.
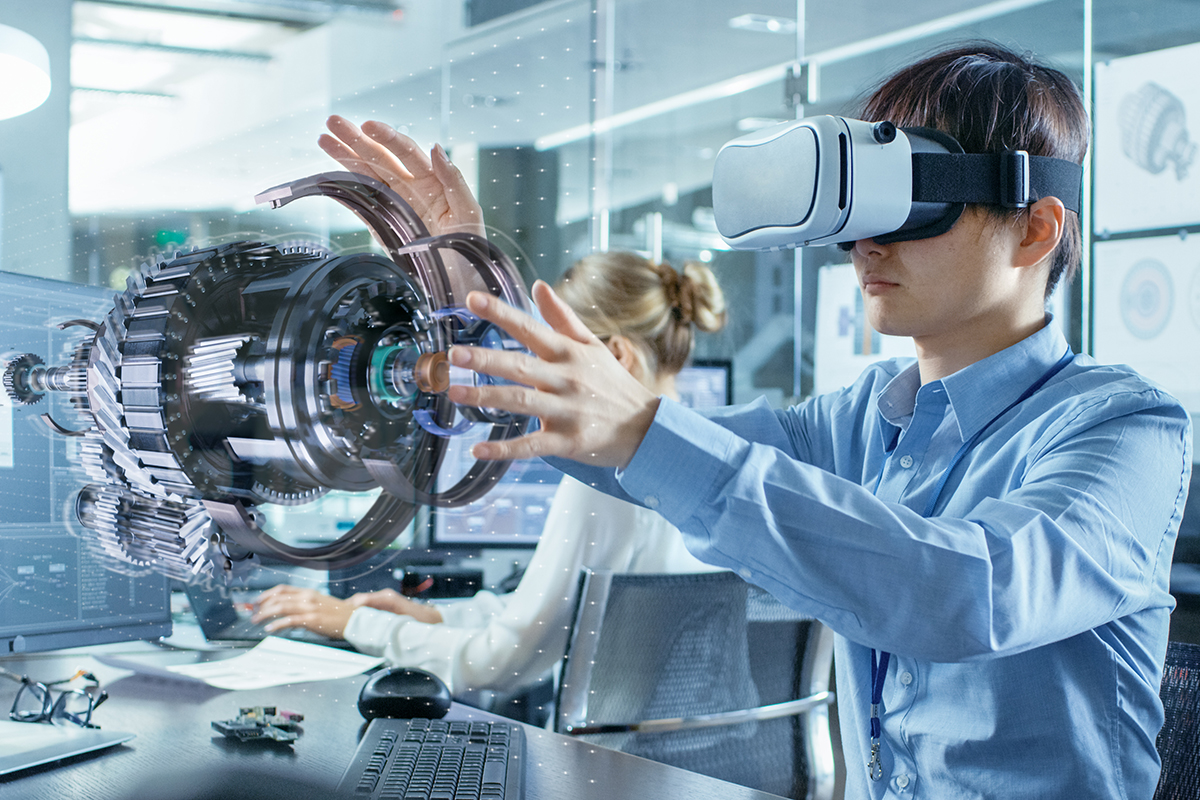
To perform the assessments, engineers use augmented reality visors. The visors enable engineers to see a machine in operation in the digital realm. The technology also allows them to adjust the orientation of objects. This process enables engineers to pinpoint defects. Some companies use digital twins to create mockups. They use the tech to emulate their entire assembly line and its parts.
With the resulting studies, these companies can carry out production more efficiently. The studies also help companies to reduce production costs. In aeronautics, engineers use digital twins to evaluate jet engine components. These assessments enable them to identify parts that are due for maintenance. It also helps them pinpoint parts that need replacement. In this way, digital twin technology can reduce maintenance costs. Furthermore, it can do the same for many complex products.
Digital Twins and the Smart Factory
Digital twins enable manufacturers to access a high-level overview of the entire operation. The technology enables them to monitor physical equipment. The resulting data provides several benefits. For instance, it helps engineers to identify problems. More importantly, engineers can find problems before they become costly emergencies.
Furthermore, digital twin technology also helps companies to plan for future opportunities. It also helps them to plan for improvements.
NASA is a perfect example of this use of digital twin technology. The agency has used the technology for years.
Engineers can’t reach equipment that’s in space. However, they can install sensors on orbiting equipment. Using digital twin technology, agency engineers collect data. They use that data to operate and monitor orbiting equipment. They also use the information to plan repairs and improvements for equipment that’s in space.
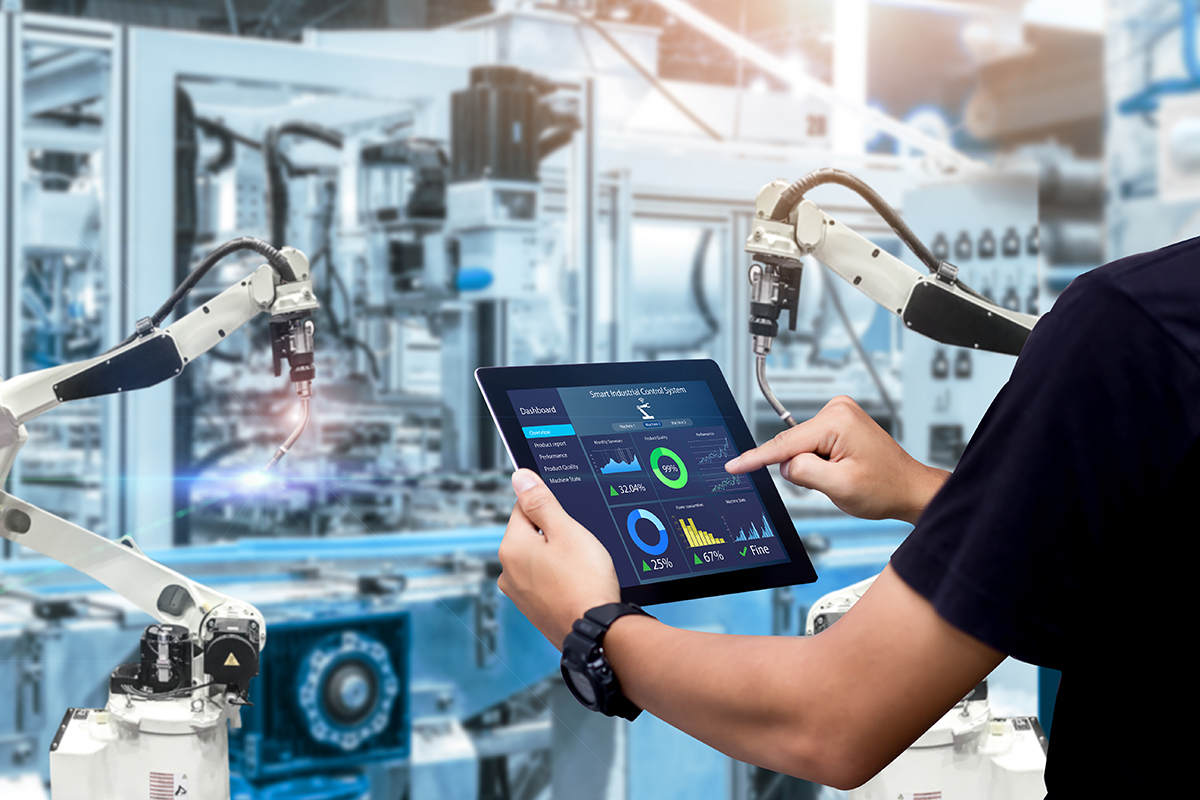
Today, smart factories deploy digital twin technology by connecting sensors to manufacturing equipment. The sensors enable engineers to monitor whether their equipment is functioning properly. Digital twin technology also helps engineers to identify inefficiencies. More importantly, it allows them to fix inefficiencies well in advance. These kinds of insights enable manufacturers to maintain increased uptime. Engineers also use digital twin technology for exhaustive testing. The technology enables engineers to simulate various scenarios. The test results enhance engineers’ ability to plan future changes.
Benefits and Advantages of the Digital Twin
Engineers have become incredibly skilled at creating realistic digital twins. It’s vital that a digital twin mimic a physical object closely. A realistic representation helps engineers can find inefficiencies. It also helps them to find opportunities.
In the manufacturing industry, equipment is highly instrumented. For this reason, engineers can more accurately simulate how devices perform over time using digital twins.
This ability can enable engineers to predict future performance. It can also help them to predict possible failures with accuracy. More importantly, it can help them to lengthen the product lifecycle of mission-critical equipment.
How the Technology of the Digital Twin Will Develop in the Future
Currently, digital twin technology is poised for an evolution. A digital twin can encompass a description of the device. It also includes a 3D rendering and details of device sensors. Also, it will generate sensor readings that simulate real-life scenarios continually.
However, a predictive twin model can forecast the future behavior and state of a device. A predictive twin bases this prediction on historical data. That data enables a predictive twin to simulate breakdowns in other pressing scenarios.
Digital twin technology doesn’t support every application. However, there are many applications for which digital twin technology is ideal. In these instances, firms can leverage digital twin technology to prepare for future challenges successfully.
Trust Us to Take Your Processes Into the Future
Now you know more about the IoT, digital twin, and smart factory technologies in the manufacturing industry. If you’re ready to improve your processes with digital twin technology, you’ll need an experienced provider.
ADTANCE specializes in digitizing after-sale services. Our software will enable you to increase efficiency and customer satisfaction.
We support clients across a wide range of industries. Over the years, we’ve worked with a wide variety of enterprises.
Our clients have ranged from special-purpose machine manufacturers to global automotive manufacturers. We can show you how to optimize your business model for maximum success.
Contact us any time. We are looking forward to hearing from you.