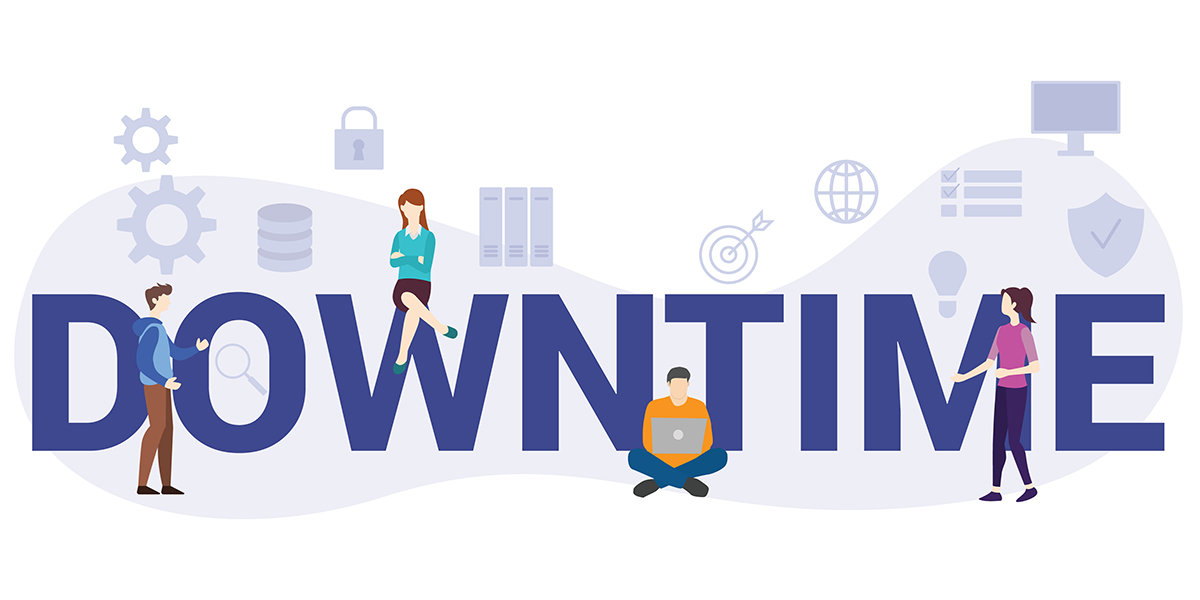
Even a one-hour unplanned downtime of a machine in a manufacturing company can cost up to USD 260000 Aberdeen. Bei einem eintägigen Maschinenausfall wären dies bereits 2 Millionen USD (entspricht ~1,7 Millionen EUR). In the automotive industry, on the other hand, an unplanned machine downtime of just one minute can cost between USD 22000-50000 (Thomas).
How are these Costs, Caused by Downtime, Composed?
The direct costs caused by downtime usually consist of the downtime, the average production rate per hour, the units not produced during a downtime and the gross profit per unit.
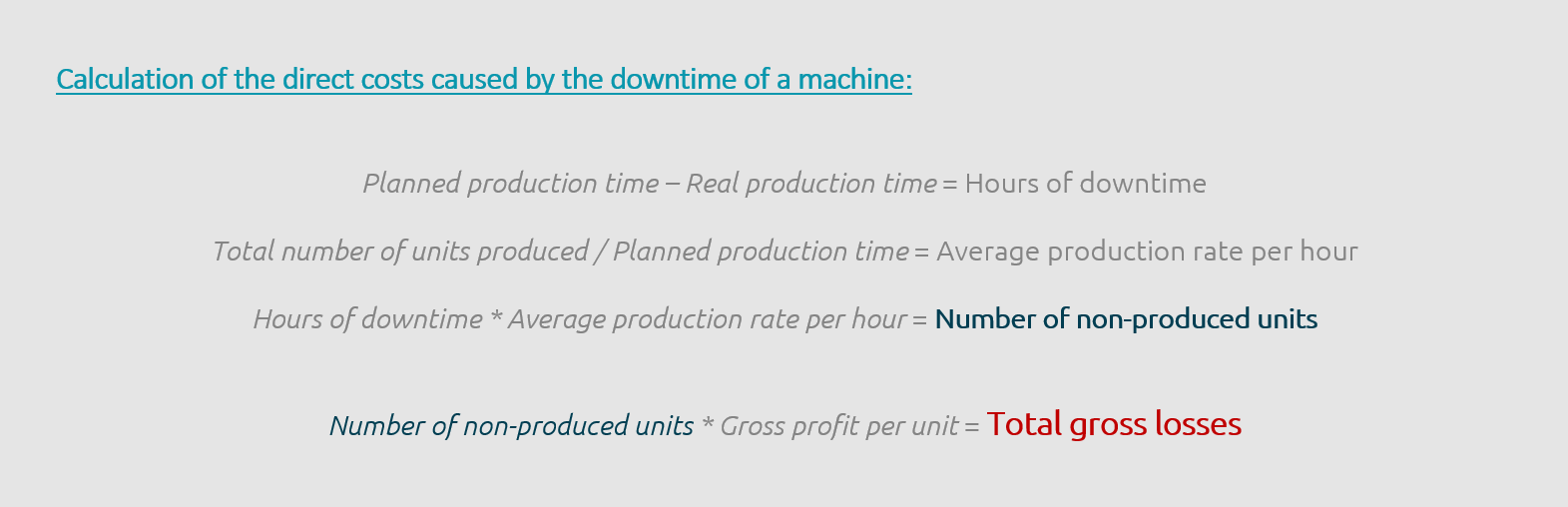
To illustrate this with a sample calculation, the costs for a 3-day machine failure are calculated below.
A 40-hour operating time and an output quantity of 15000 units per week are assumed. The gross profit per unit should be $8.
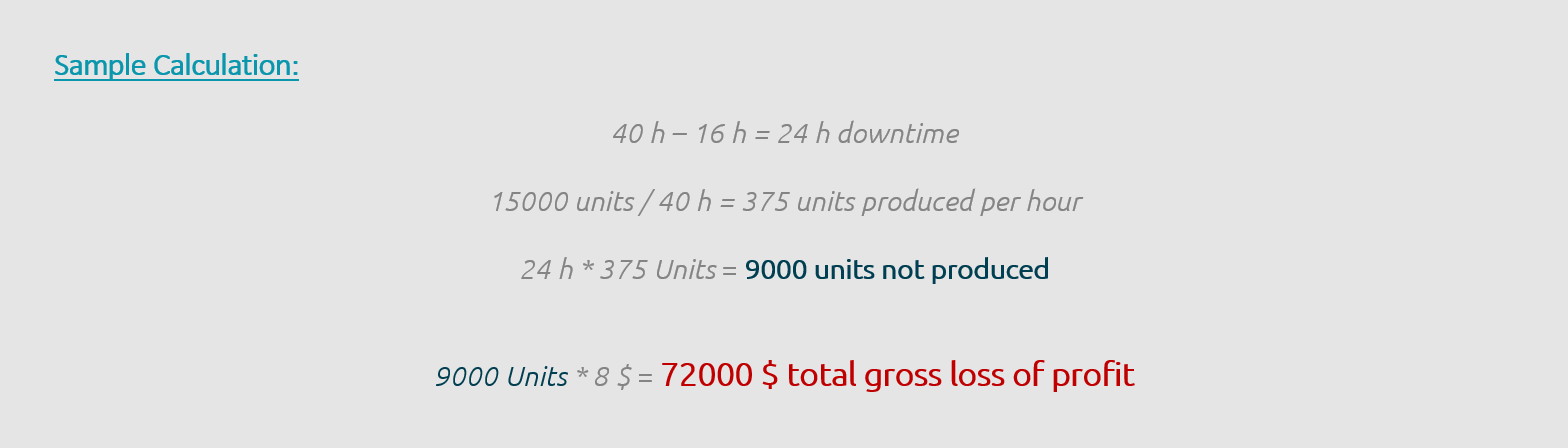
According to this calculation example, the gross profit loss of a machine after a standstill of three days already amounts to $72,000.
However, the following must be considered: This calculation only includes the loss of profit due to the downtime. Added to this are the costs for a technical expert who carries out the repair of the machine. It must also be considered that production employees must continue to be paid, even though they cannot continue to work on the machine during the downtime. These and further costs are listed and described in detail below.
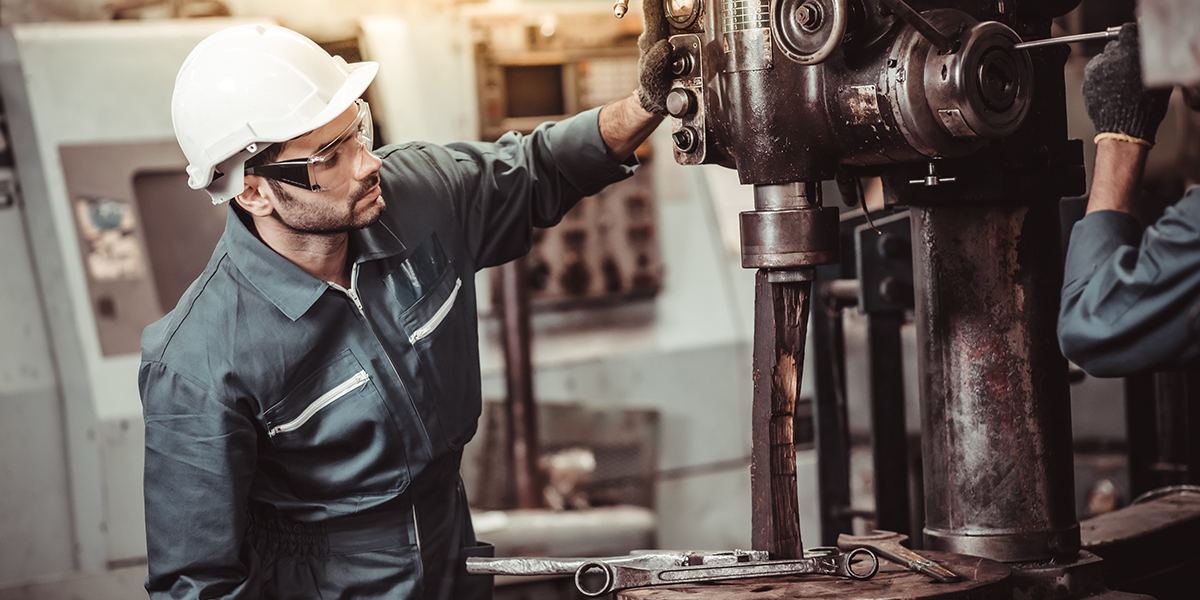
Various Costs Arising from a Machine Downtime
Costs of Error Identification
These are all costs related to the investigation and identification of the defect. This includes the time, personnel and resources required to detect and diagnose the problem.
Cost of Containing the Problem
This includes those costs associated with the activities that enable the company to reduce the impact of the unexpected downtime. It prevents the defective equipment from affecting other assets. This includes the cost of implementing temporary solutions until a permanent solution can be found.
Recovery Costs and Third-party Costs
Recovery costs are costs associated with restoring business operations to their original condition. Specialists must be called in to resolve the problem and the resources required for the repair must be paid.
Costs Associated with Loss of User Productivity
These are costs associated with the loss of user productivity. Due to the failure of the machine, the relevant employees cannot perform their work, but must still be paid. Other costs included in this cost pool are overtime costs that are necessary to compensate for the lost work.
Costs due to Lost Earnings
This is the total revenue lost as a direct result of machine downtime. These are the units or products that are not manufactured and therefore cannot be sold or sold with a delay (cost block of the example calculation).
Total Costs of the Business Interruption
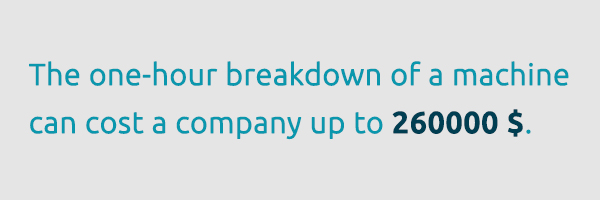
These are the comprehensive costs of equipment downtime, including lost revenue, lost productivity, recovery costs, but also costs resulting from potential damage to the company's reputation, missed deadlines, customer churn and long-term damage to business systems and processes.
In summary, however, probably the greatest loss is caused by the lost time when the machine is not running and producing no output.
What are the Reasons for Unforeseen Downtime?
On the one hand, unplanned downtimes of machines and systems can occur due to improper or missing maintenance. Second, a study by Vanson Bourne, sponsored by ServiceMax, shows that human error is the most common cause of such downtime.
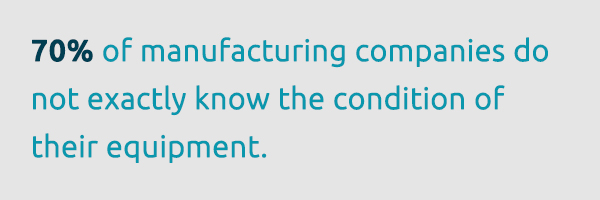
70% of the manufacturing companies surveyed do not know the exact condition of their equipment or when it needs to be serviced, upgraded or replaced. Another common reason is lack of equipment that can tell companies when their equipment needs to be serviced or replaced.
The Vanson Bourne study surveyed 100 companies in the manufacturing sector as well as 350 companies in the medical, oil & gas, energy & utilities, telecommunications, distribution, logistics and transportation industries on issues related to equipment downtime.
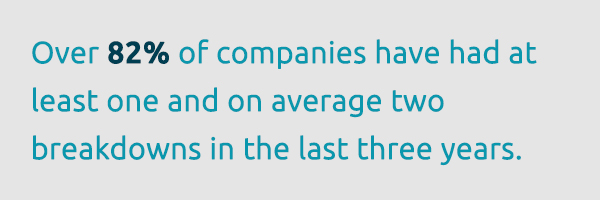
Across all sectors, 82% of the companies have experienced at least one and on average two unplanned outages in the last three years.
However, unplanned downtime caused by user error is significantly higher in the manufacturing industry (23%) than in the other sectors (9%). This means that the manufacturing sector and its productivity of machinery and equipment is the sector most affected by unplanned downtime. However, this is by no means due to a lower level of employee competence in this industry, but rather to the broad mass of machines that require maintenance and inspections by service technicians and are not yet equipped with the appropriate technology that could prevent such downtimes.
As a result, many companies in the manufacturing sector still have to deal with unplanned downtime and the impact this has on the efficiency and output of the entire production process.
How can Unplanned Downtimes be Avoided?
There are already various digital service offerings on the market that ensure fast and, in some cases, even automated field service management. Among other things, such software solutions can use sensors to continuously measure the condition of the machine and trigger an alarm as soon as deviations are detected. In this way, tight deadlines can be met and corrective measures can be taken before serious problems, malfunctions and breakdowns occur.
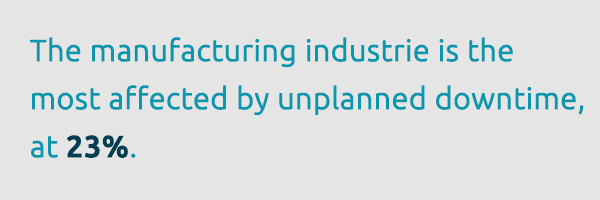
Such digital offers for the maintenance of machines and plants to avoid long downtimes and high losses are used by some but not yet by the majority of manufacturing companies.
However, companies have the goal of going digital: For 72% of the companies surveyed, zero unplanned downtime is the number one priority or at least has high priority. According to this, the problem is increasingly being addressed and companies want to use digital capabilities to shift service measures, error and problem resolution from reactive to proactive and thus to predictive measures.
Digital Service Offerings for Optimized Service Processes on Machines and Systems
We at ADTANCE are also offering various digital solutions for optimised service processes, the maintenance, servicing and inspection of machines to reduce or completely avoid downtime.
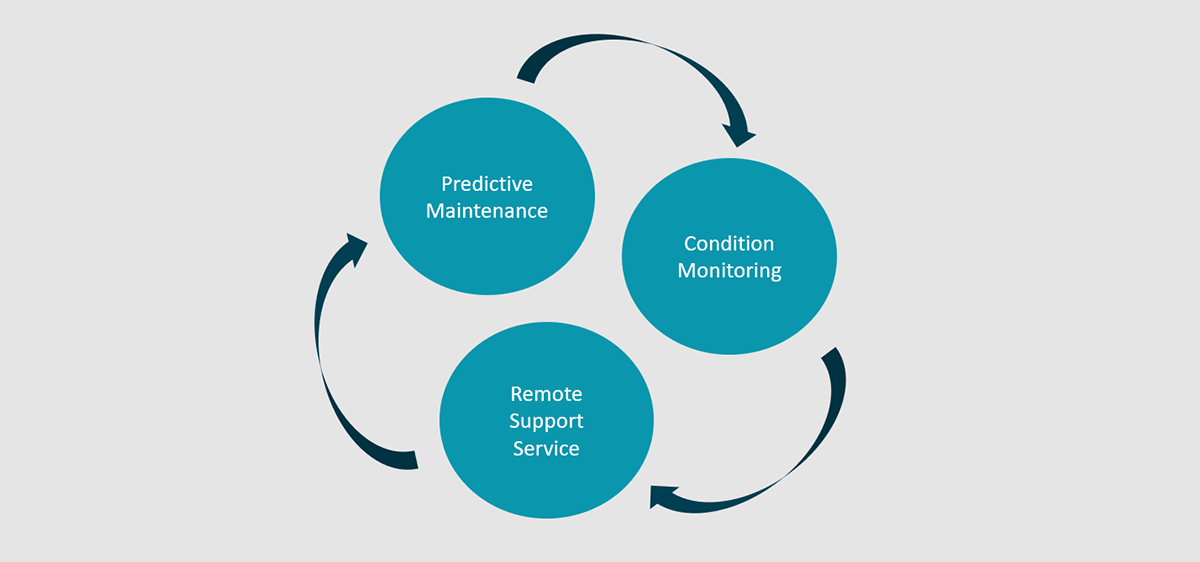
These include ADTANCE Support, ADTANCE Predictive Maintenance and ADTANCE Visualisation & Monitoring.
With ADTANCE Support, service experts can be contacted directly if a problem with the machine occurs. The expert can then take a direct virtual look at the source of the problem using video live chat. The worker on site can then, in most cases, correct the defect directly with the help of the service expert's instructions.
You can read more about the so-called Remote Service in our 2nd part of the article series "Digitalization of After Sales Service" regarding the topic Support Service with data glasses.
ADTANCE Visualisation & Monitoring is a type of condition monitoring. It enables you to monitor machines in real time. This allows statements to be made about the safety and efficiency of the machine. The results of the condition monitoring can be viewed using various mobile devices such as tablets, smartphones or computers.
With ADTANCE Predictive Maintenance, various machine parameters can be automated and permanently monitored to identify problems that may occur in the future. The software automatically sounds an alarm if there are deviating measurements.
Learn more about Condition Monitoring & Predictive Maintenance in our 3rd part of the series " Digitalisation of After Sales Service".