Digitalization has taken on a significant role in mechanical engineering in recent years, revolutionizing the way companies in this industry operate. From the introduction of IoT technologies to the implementation of Big Data analytics and machine learning, digital transformation presents a multitude of opportunities and challenges for mechanical engineering. In this article, we will look at the different aspects of digitalization in mechanical engineering and how companies can benefit from this development.
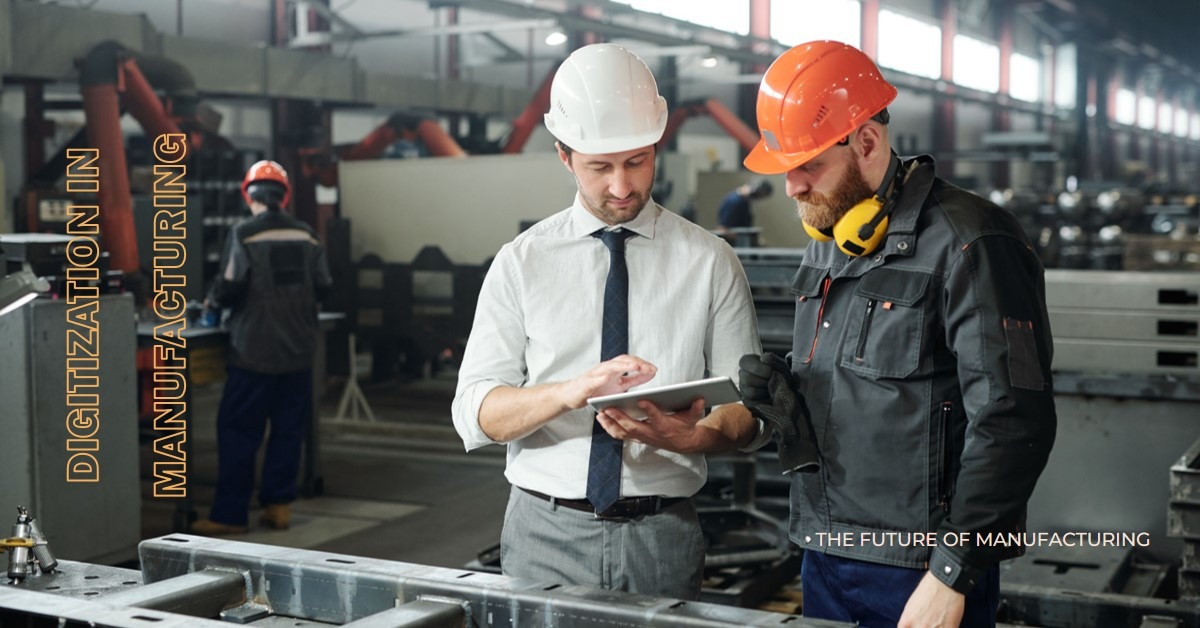
Introduction to digitization in mechanical engineering
What is digitization in mechanical engineering?
Digitization in mechanical engineering refers to the use of advanced technologies and digital solutions to improve production processes, efficiency and performance of machines. This includes the use of IoT technologies, Big Data analytics, machine learning and the implementation of Industry 4.0 concepts.
Importance of digitalization in mechanical engineering
The importance of digitization in mechanical engineering cannot be underestimated. It enables more efficient production, improved product quality, optimization of maintenance processes and the creation of new business opportunities. Companies that do not rise to the challenges of digitization risk being left behind by the competition.
Advantages of digitization in mechanical engineering
Digitization in mechanical engineering offers numerous advantages. These include increasing productivity and efficiency, improving process reliability, reducing downtime, enabling products to be customized, opening up new markets and reducing production costs. Companies can become more competitive and future-proof through digital transformation.
Use of IoT technologies in mechanical engineering.
The use of IoT technologies in mechanical engineering has changed the way companies design, manufacture and maintain machines. IoT enables the networking of machines and devices, the collection of large amounts of data and communication between individual components.
IoT technologies at a glance
IoT technologies include sensors, actuators, network connectivity and cloud platforms. Sensors capture data such as temperature, pressure, vibrations and enable monitoring and control of machines. Actuators enable remote activation of devices. Network connections enable communication between components, while cloud platforms enable processing and analysis of large amounts of data.
Applications of IoT in mechanical engineering
The applications of IoT in mechanical engineering are diverse. Companies can predict maintenance needs and reduce unplanned downtime by monitoring machines in real time. Remote maintenance of machines enables experts to diagnose problems remotely and offer solutions. In addition, IoT can be used to optimize production processes, monitor the supply chain, and improve energy efficiency.
Advantages of using IoT in mechanical engineering.
The use of IoT in mechanical engineering offers numerous benefits. These include improving machine performance, reducing maintenance costs, increasing uptime, improving customer satisfaction, preventing production downtime, and optimizing supply chain processes. Companies can strengthen their competitiveness and develop innovative solutions through the use of IoT technologies.
Big Data and machine learning in mechanical engineering.
The availability of big data and the use of machine learning have led to new opportunities in mechanical engineering. Big Data enables the collection, storage and analysis of big data, while machine learning develops algorithms and models to identify patterns and relationships in the data.
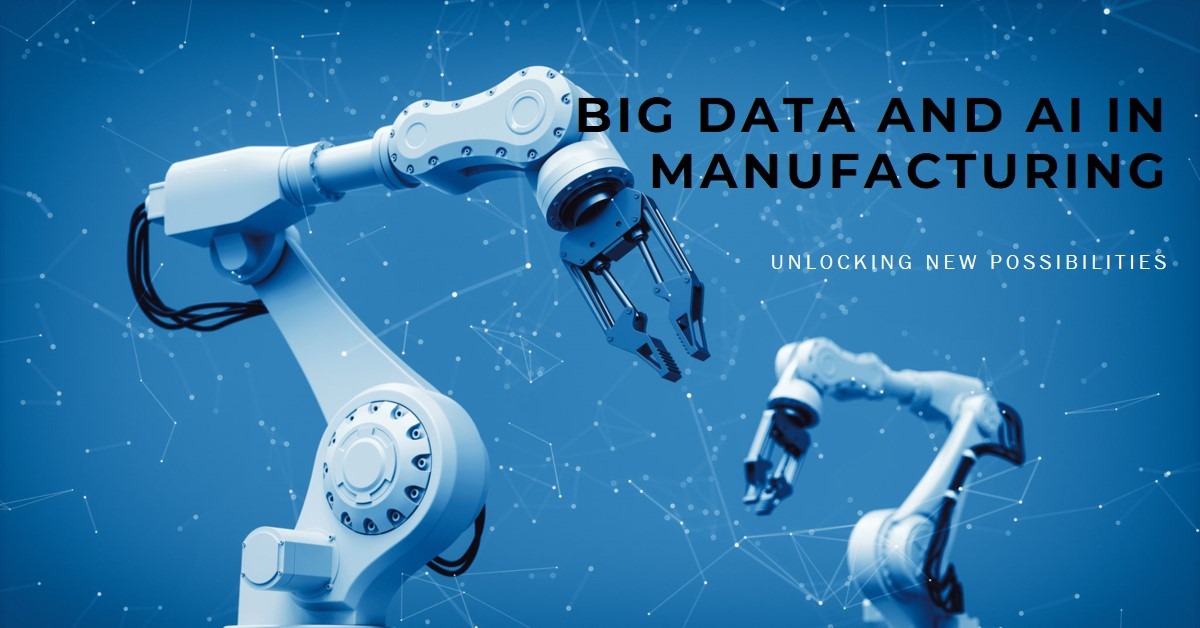
Importance of Big Data in Mechanical Engineering
Big Data offers valuable insights and information in mechanical engineering. By analyzing large amounts of data, companies can identify trends, optimize processes, predict maintenance needs, and improve product quality. Big Data also makes it possible to make decisions based on data and develop sound business strategies.
Applications of Big Data and machine learning in mechanical engineering.
Big Data and machine learning are finding application in mechanical engineering in a number of areas. Companies can increase efficiency and reduce costs by analyzing production data. Machine learning can be used to develop models for predictive maintenance, optimize production processes and improve quality controls. In addition, data analytics can be used to identify customer needs and develop customized products.
Improving processes and efficiency through Big Data and machine learning.
By using Big Data and machine learning, companies in the mechanical engineering sector can significantly improve their processes and efficiency. Bottlenecks and inefficient processes can be identified by analyzing production data. Machine learning can be used to develop optimization algorithms that improve production flow and optimize resource utilization. This leads to increased productivity, lower costs and improved competitiveness.
Industry 4.0 and the future of mechanical engineering
Industrie 4.0 stands for the fourth industrial revolution and refers to the integration of digital technologies into industrial production. In mechanical engineering, Industrie 4.0 has the potential to revolutionize the way machines are developed, produced and operated.
What is Industry 4.0?
Industry 4.0 involves the use of IoT technologies, artificial intelligence, cloud computing, robotics and other digital solutions. The networking of machines, products and people results in intelligent production in which various components communicate with each other and can act in a self-organized manner.
Impact of Industry 4.0 on mechanical engineering
Industry 4.0 has a variety of implications for mechanical engineering. By integrating digital solutions, companies can act more flexibly and agilely. Production becomes more efficient and the quality of products increases. In addition, Industrie 4.0 enables individualized production, where products are manufactured according to the specific requirements of customers. This opens up new business opportunities and enables better customer retention.
Future prospects and potential of Industrie 4.0 in mechanical engineering
The future prospects of Industrie 4.0 in mechanical engineering are promising. With the further development of IoT technologies, artificial intelligence and robotics, automation will continue to advance. This will lead to higher efficiency, lower production costs and increased competitiveness. In addition, new business models are opening up, such as the use of data-based services and predictive maintenance.
Challenges and risks of digitization in mechanical engineering.
Although digitization in mechanical engineering offers many advantages, there are also challenges and risks that companies should be aware of.
Security and data protection
With increasing networking and the exchange of data, the importance of security and data protection is growing. Companies must ensure that their systems are protected against cyber attacks and that sensitive data is protected against unauthorized access. Protecting data integrity and customer privacy are crucial factors for the success of digital solutions in mechanical engineering.
Skilled labor shortage and qualification
Digital transformation requires specialized knowledge and qualified personnel. However, mechanical engineering often faces a shortage of skilled workers. Companies need to invest in the education and training of their employees to ensure that they have the necessary skills to successfully use digital technologies.
Investment costs and risks
Implementing digital solutions in mechanical engineering often requires significant investment. Companies need to consider the costs of purchasing technologies, converting processes and training employees. In addition, every new technology also carries a certain level of risk. There is a possibility of bad investments or technical problems that can affect operations.
Success factors for digital transformation in mechanical engineering.
For companies to successfully implement digital transformation, there are some success factors that should be considered.
Digital strategy and roadmap
It is important to develop a clear digital strategy and roadmap. Companies should define what goals they want to achieve with digitalization and how they can implement these goals. Thoughtful planning helps to deploy resources efficiently and ensure the success of the digital transformation.
Collaboration and networking
Digital transformation requires close collaboration and networking between different departments and partners. It is important that the various stakeholders work together and share their knowledge and experience. This promotes the exchange of best practices and enables a holistic view of digitalization in mechanical engineering.
Flexibility and agility
Digital transformation requires flexibility and agility. Companies should be open to change and able to adapt quickly to new technologies and market conditions. This requires a culture of experimentation and continuous learning.
Continuous development and innovation
Digital transformation is an ongoing process. Companies should continuously evaluate new technologies and solutions and develop innovative ideas. By integrating new technologies and continuously improving processes, companies can remain competitive and reap the benefits of digitization in mechanical engineering.
Case studies of successful digitization projects in mechanical engineering.
There are numerous examples of companies that have successfully implemented digital technologies in mechanical engineering. These examples have already been implemented with the ADTANCE Smart Service Platform.
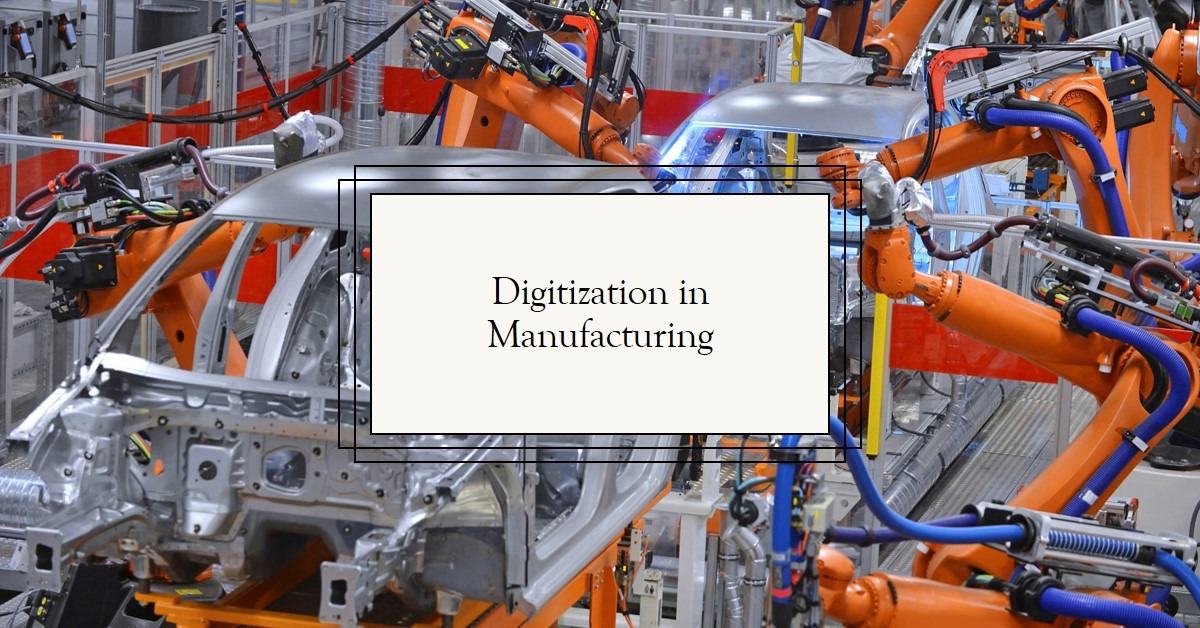
Case study 1: Optimizing production through IoT and predictive maintenance.
A medium-sized company in the mechanical engineering sector has recognized that it needs to make its production processes more efficient in order to remain competitive. It decides to implement IoT technologies and predictive maintenance to optimize production.
The company starts by placing sensors on its machines to collect real-time data about their condition and performance. This data is transmitted to the cloud via a secure network connection. There, it is analyzed using data analytics tools.
By analyzing the data, the company can detect deviations and anomalies in real time. As a result, potential machine failures can be predicted and avoided at an early stage. The company is implementing a predictive maintenance system that automatically schedules and performs maintenance when needed, rather than relying on a set schedule.
Optimizing production through IoT and predictive maintenance results in significant improvements. Machines run longer and more reliably, leading to an increase in overall equipment effectiveness (OEE). In addition, maintenance costs are reduced as unplanned downtime is minimized.
By successfully implementing these digital solutions, the company is able to increase its competitiveness, improve customer satisfaction and consolidate its position as an innovation leader in mechanical engineering.
Case study 2: Increasing efficiency through Big Data analyses and machine learning
A global engineering company wants to further optimize its production processes in order to work more efficiently and reduce costs. It decides to use Big Data analytics and machine learning to achieve these goals.
The company collects extensive data about its production operations, quality assurance, and supply chain processes. This data is stored in a central database and analyzed using Big Data analytics tools.
By analyzing the data, the company identifies bottlenecks and inefficient processes. It develops optimization algorithms using machine learning to improve these processes. The algorithms are trained to recognize patterns and relationships in the data and automatically generate optimization suggestions.
By implementing the optimization algorithms, the company is able to optimize production processes, eliminate bottlenecks and improve resource utilization. As a result, productivity increases, lead times are shortened and costs are reduced.
The company achieves significant savings and improved competitiveness through increased efficiency. It can make informed decisions based on data and continuously optimize its processes to meet changing market demands.
Case study 3: Introduction of Industry 4.0 concepts for product individualization
A renowned company in the mechanical engineering sector wants to drive product individualization and offer customers customized solutions. It decides to introduce Industrie 4.0 concepts to achieve these goals.
The company integrates IoT technologies and networks its machines to collect real-time data about the production process. This data is stored in the cloud and can be accessed at any time.
By networking the machines, the company can track production progress in real time. Customer requirements and individual specifications are integrated into the production system to produce customized products. Production becomes more flexible and can respond to individual customer requests.
The company is also implementing a digital order management system that enables customers to check their track orders online and the status of their products in real time. This increases transparency and customer satisfaction.
By introducing Industrie 4.0 concepts for product individualization, the company can offer its customers customized solutions. This leads to increased customer satisfaction, higher customer loyalty and a differentiated positioning compared to the competition.
Conclusion
Digitalization offers great opportunities for mechanical engineering. By leveraging IoT technologies, Big Data analytics, machine learning, and Industry 4.0 concepts, companies can increase efficiency, improve product quality, and unlock new business opportunities. However, it is important to consider the challenges and risks of digitalization and to implement the right success factors. Companies that successfully implement digital transformation can strengthen their competitiveness and meet the future demands of the engineering industry.
Frequently asked questions
1. What role do IoT technologies play in mechanical engineering?
IoT technologies play a crucial role in mechanical engineering. They enable the networking of machines, the collection of data and the optimization of processes. By using IoT technologies, companies can increase productivity, improve maintenance and open up new business opportunities.
2. How can Big Data be used in mechanical engineering?
Big Data offers a wide range of opportunities in mechanical engineering. Companies can analyze large amounts of data to identify trends, optimize processes and improve product quality. Big Data also makes it possible to make data-based decisions and develop sound business strategies.
3. What are the main challenges in digitization in mechanical engineering?
Digitization in mechanical engineering brings with it a number of challenges. These include security and data protection, the shortage of skilled workers, and high investment costs. Companies must actively address these challenges to ensure a successful digital transformation.
4. What is Industrie 4.0 and how does it affect mechanical engineering?
Industrie 4.0 refers to the integration of digital technologies into industrial production. In mechanical engineering, Industrie 4.0 has the potential to improve the efficiency, flexibility and quality of production. By networking machines and using data, companies can optimize their processes and develop innovative solutions.
5. How can companies successfully implement the digital transformation?
To successfully implement digital transformation, companies should develop a clear digital strategy and roadmap, work closely with various stakeholders, be flexible and agile, continuously innovate and evolve. These success factors are crucial for making the most of the benefits of digitalization in mechanical engineering.