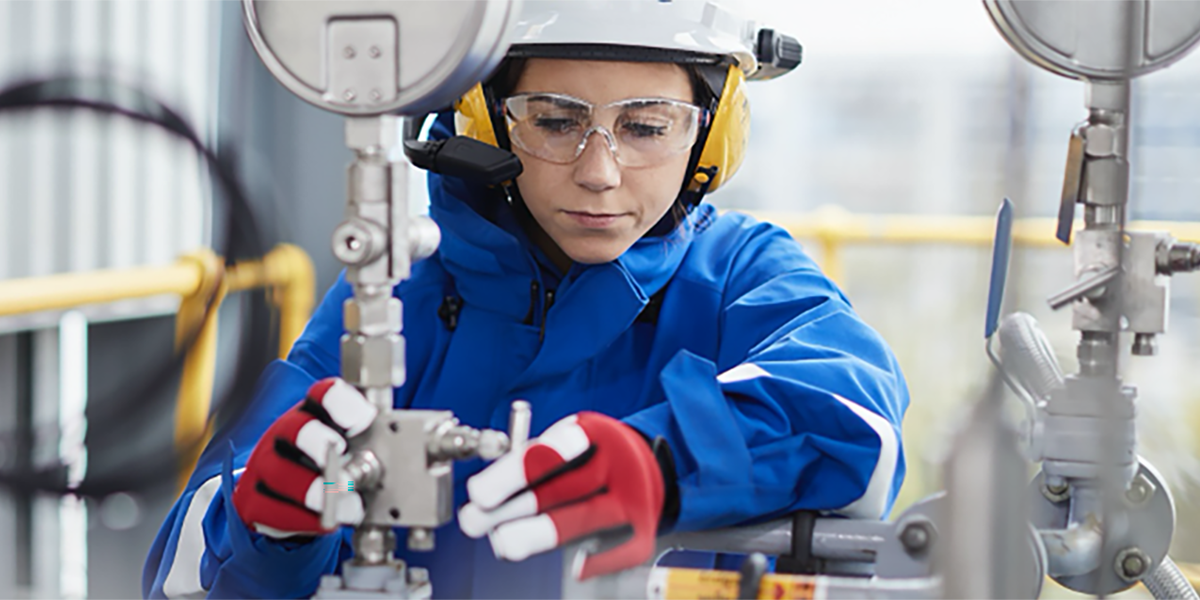
For prospective and current manufacturers alike, one of the many lessons the recent pandemic has taught manufacturers is that remote commissioning is here to stay. Multiple companies have found that implementing digital troubleshooting and maintenance into their facility's processes has been a valuable optimization tool. Those attaching remote commissioning capabilities to their devices are experiencing faster troubleshooting, fewer employee expenses and are better equipped to advise their clients on how to optimize their engineering processes, while downstream manufacturers utilizing their services enjoy drastically reduced machine downtime, subsequent unit production increases, and elimination of the need for a technician. We'll first take a look at what remote commissioning is and how it works, followed by a deeper dive into the benefits a facility can expect along with some data to evaluate whether the investment is worthwhile.
How it Works
The best way to conceive of remote commissioning is to consider on-site project commissioning first. On most production sites, a construction firm is required to establish the functionality of all systems and components before client handover, and is responsible for periodic maintenance and inspection as well. When performed remotely, as has been the case for many manufacturers whose production has continued during the pandemic, service technicians and field personnel were equipped with remote technology such as apps, videoconferencing, and smart hardware so that they could commission and maintain machines without the presence of another technician.
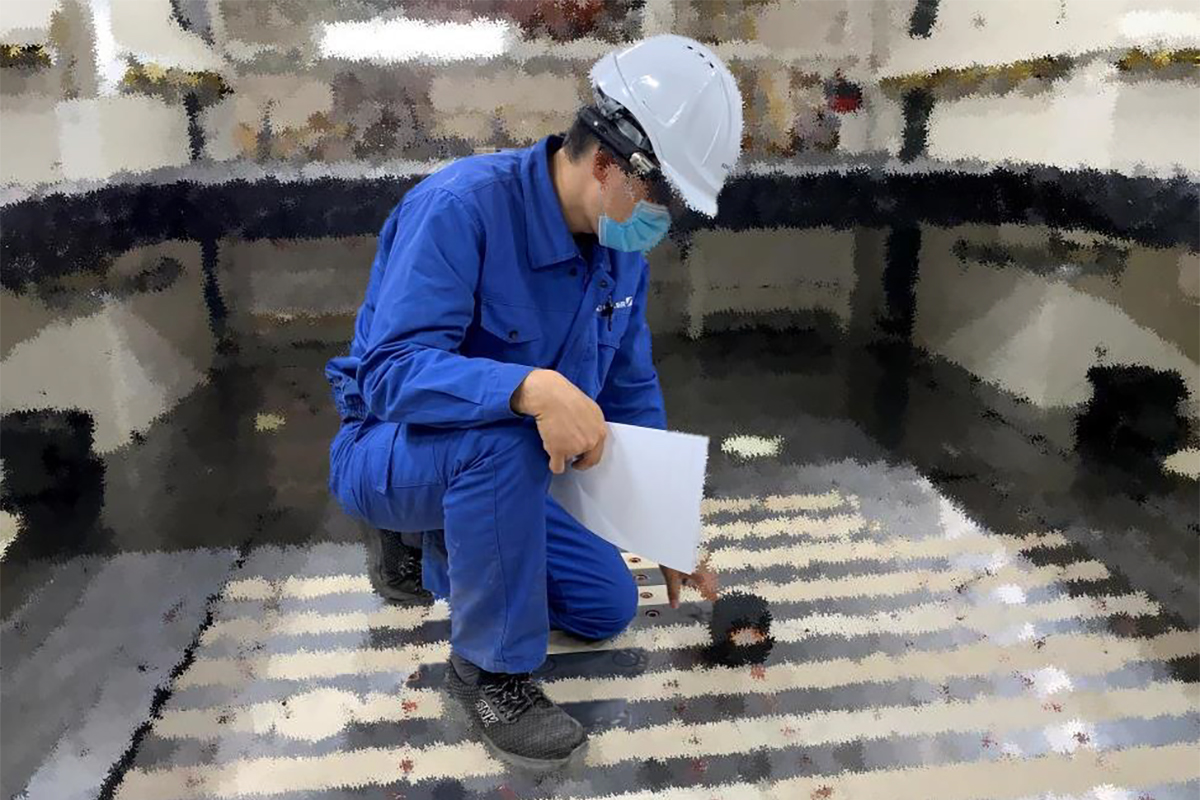
Of course, someone has to be on the factory floor to perform any physical repairs that may be necessary, but technology has enabled engineers with more in-depth knowledge of their machines to be nearly present to assist on-site personnel in any required troubleshooting and maintenance.
The use of ADTANCE's data glasses provides those present at the facility with an enhanced-reality experience, delivering not only machine specifications and blueprints to the user for any component they're looking at, but also relaying a live image to the service technician who has a deeper understanding of the device from their remote office.
With a one-time investment in the software and hardware required for remote commissioning to work, the presence of a traveling maintenance engineer is eliminated - as well as the burdens that come with it.
Metrics
Manufacturers that have capitalized on remote commissioning have seen that this technology isn't just a health-conscious trend amidst a pandemic; it's a way to maximize growth. Here are a few business outcomes that companies implementing remote servicing have noticed which have become metrics of success.
- Reduced travel costs - Remote commissioning enables service technicians to put their knowledge on the facility floor without being physically present. As such, companies will no longer incur wasteful travel expenses to put their technicians on site. The cost of sending an engineer to the facility, paying for their fare, stay, and associated living expenses adds up significantly, and this burden is drastically reduced (if not eliminated entirely) when technicians can troubleshoot or maintain their equipment remotely. If you're utilizing remote commissioning, your repair-related travel expenses should be next to zero.
- Shorter response times - It takes time to get a technician on the manufacturing ground, and each delay results in machine downtime and lost profits. When technicians are able to view the problem and are fed all data as though they were already there, there is no longer a need for lengthy commutes to evaluate devices in-person, and equipment can be repaired in a fraction of the time. If you employ remote commissioning, expect a reduction in your response times.
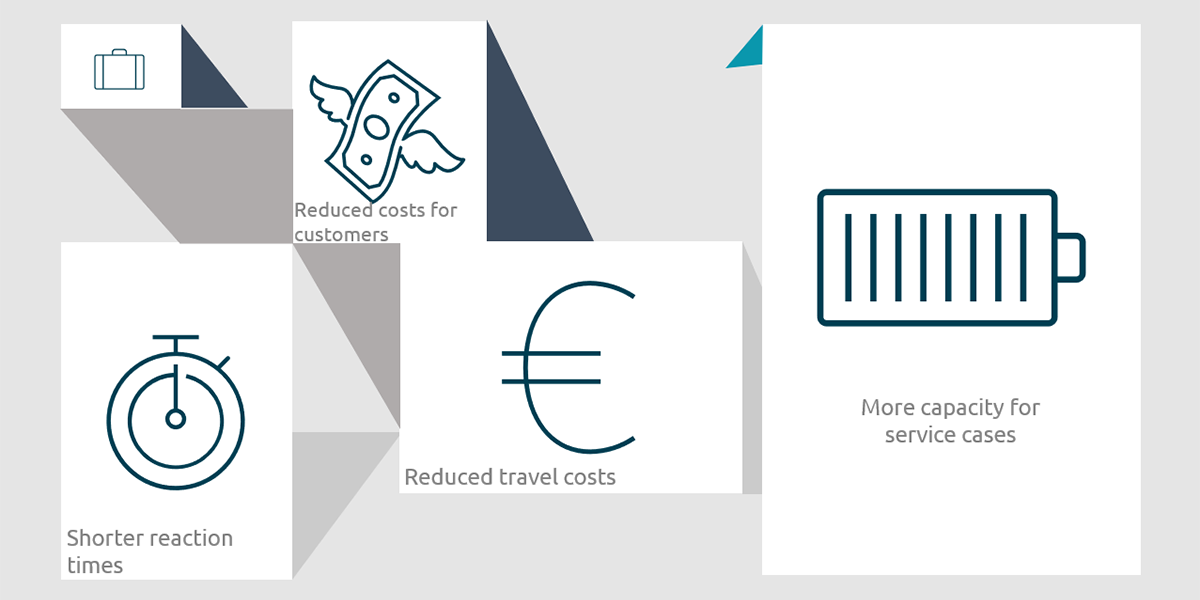
- Higher case capacity - Without the need for service engineers to travel from location to location troubleshooting one facility at a time, a single technician may assume a greater workload of service cases. By implementing remote commissioning, suppliers may service products across the globe in a single day, when it would have taken weeks or months to achieve the same tasks in person. Companies that make the most of remote servicing are able to increase their service capacity, and are able to repair more equipment with the same number of technicians.
- Lower customer costs - With the cost of a service technician all but removed, suppliers are able to pass the savings along to their customers, making for a less expensive (and therefore more marketable) machine. One metric of successful remote commissioning is a cheaper product.
While remote commissioning certainly has its share of benefits on the supply side, most of them culminate in the same thing: customer satisfaction. Shorter and more flexible response times result in reduced machine downtime for the customer, resulting in preserved unit production and salvaged profit. With these outcomes, customers are sure to express higher satisfaction and greater interest in the supplier's equipment than they would in a company where the longer response times associated with an on-site technician was the norm.
Case Study
As an example of the return on investment a manufacturer will experience from implementing remote servicing, consider the following calculation:
- A robotics company employs 10 service engineers to make traveling repairs on their equipment. Each is sent to a different customer once a month, and stays for 5 days at a time.
- The average round-trip flight in 2020 is $336 according to the Bureau of Transportation Statistics, while the average hotel stay costs 100 dollars per night.
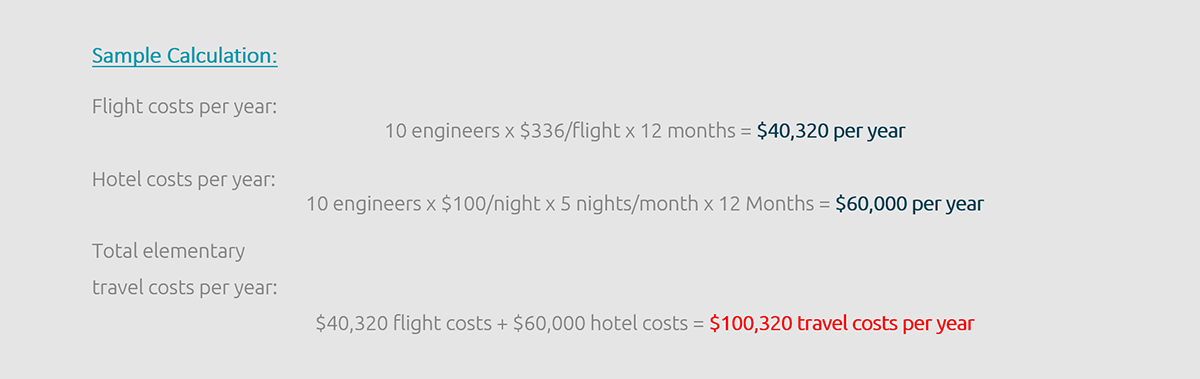
The above drastically oversimplified calculation demonstrates how quickly even the rarest essential traveling costs add up, and neglects miscellaneous costs like overtime pay, alternative productivity, etc.
Contrast that with a company that implements remote commissioning, and the benefit quickly becomes evident. Suppose the same company invested remote servicing software and smartglasses for all 10 service engineers. While actual prices may vary, if 10 smartglasses were purchased at $5,000 each along with the necessary software, the investment would pay for itself in 6 months time on savings from flight and hotel costs alone. Add to that the benefit of being able to offer customers shorter and more flexible response times, and the competitive advantage becomes clear.
Outcomes
Remote servicing carries with it the benefit of optimized production during startup, as well as greater capacity for fine tuning once production is online. Here's how:
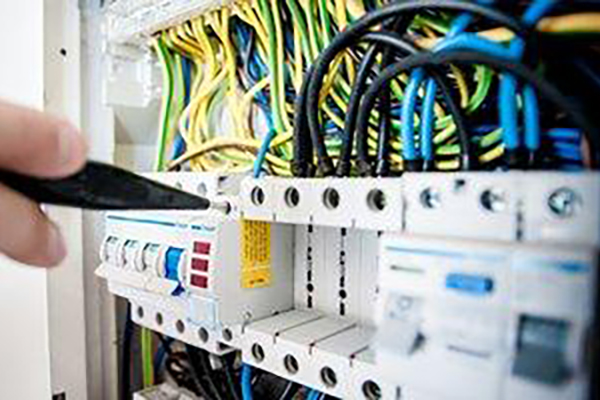
- Easier optimization - A facility will be able to more uniformly establish and reach its initial operating conditions at launch when doing so remotely, and will more precisely adjust its machinery as they attempt to optimize their manufacturing processes along the way.
- Expert Recommendations - Where predictive maintenance falls short, the data received by service technicians enables them to detect not only potential problem with their equipment, but also opportunities for further improvement. By passing along their knowledge of the machine's capabilities to the customer via support, the manufacturer can suggest operating conditions that will safely lead to improved production.
Overview
The current global pandemic has served as Exhibit A for the benefits of remote commissioning, as many companies that would otherwise have ceased to exist were able not only to continue, but thrive. Their reason for implementing remote servicing at the time may have been partially health and safety-related, but in the process they discovered that their manufacturing processes, customer service and profit margins were improved by doing so. Because of shorter, more flexible response times, customers were able to have their equipment repaired in a more timely fashion thus saving them time and money, while service engineers and technicians were empowered to take on more service cases without the need for increased travel. The investment required to implement remote commissioning technology in the form of software utilizing video live stream and data glasses is quickly offset by savings from even the most basic of travel costs, and technicians are empowered to make recommendations to customers on how best their machines may be operating to achieve maximum productivity.
Reduced travel costs, shorter response times, higher service capacity, greater customer satisfaction, and deeper customer-supplier synergy are business outcomes every manufacturer hopes to achieve, and ADTANCE provides it with ADTANCE Support. If you're ready to see how those benefits will enhance your and your customers' manufacturing capabilities, we'd love to show you just how much we can help. In today's climate, it may be difficult to survive without it.